Sintered PP Filter
High-quality polypropylene(PP) is used as the main raw material and sintered by scientific formula, which is compact, strong, light and can withstand high filtration pressure, and the aperture of the cartridge is the same inside and outside, so it is easy to blow back and de-flow, and has good corrosion resistance to acid and broken solvent.
Personalized customization:
Whether choosing from these specifications or presenting your unique requirements, Lvyuan ensures a tailored approach to meet your specific needs.
After-Sales Service and Warranty:
We offer comprehensive after-sales services, including installation guidance and technical support. Our products also come with a specified warranty period to ensure a worry-free experience for our customers.
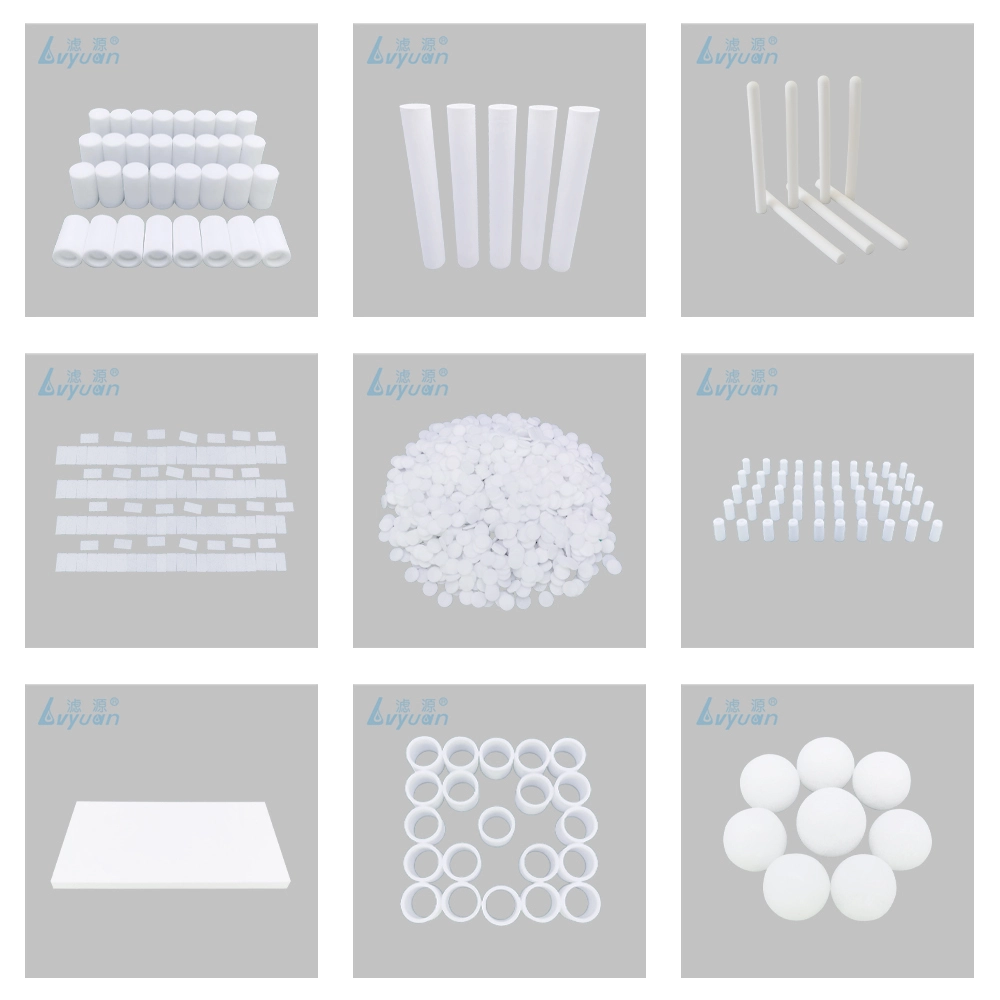
Product description
High-quality polypropylene is used as the main raw material and sintered by a scientific formula, which is compact, strong, light, and can withstand high filtration pressure. The aperture of the cartridge is the same inside and outside, so it is easy to blow back and de-flow, and it has good corrosion resistance to acid and broken solvent. Polypropylene (PP) sintered products include PP sintered cartridge, PP sintered sheet and screen plate, PP sintered filter ball, PP sintered shaped parts, etc.
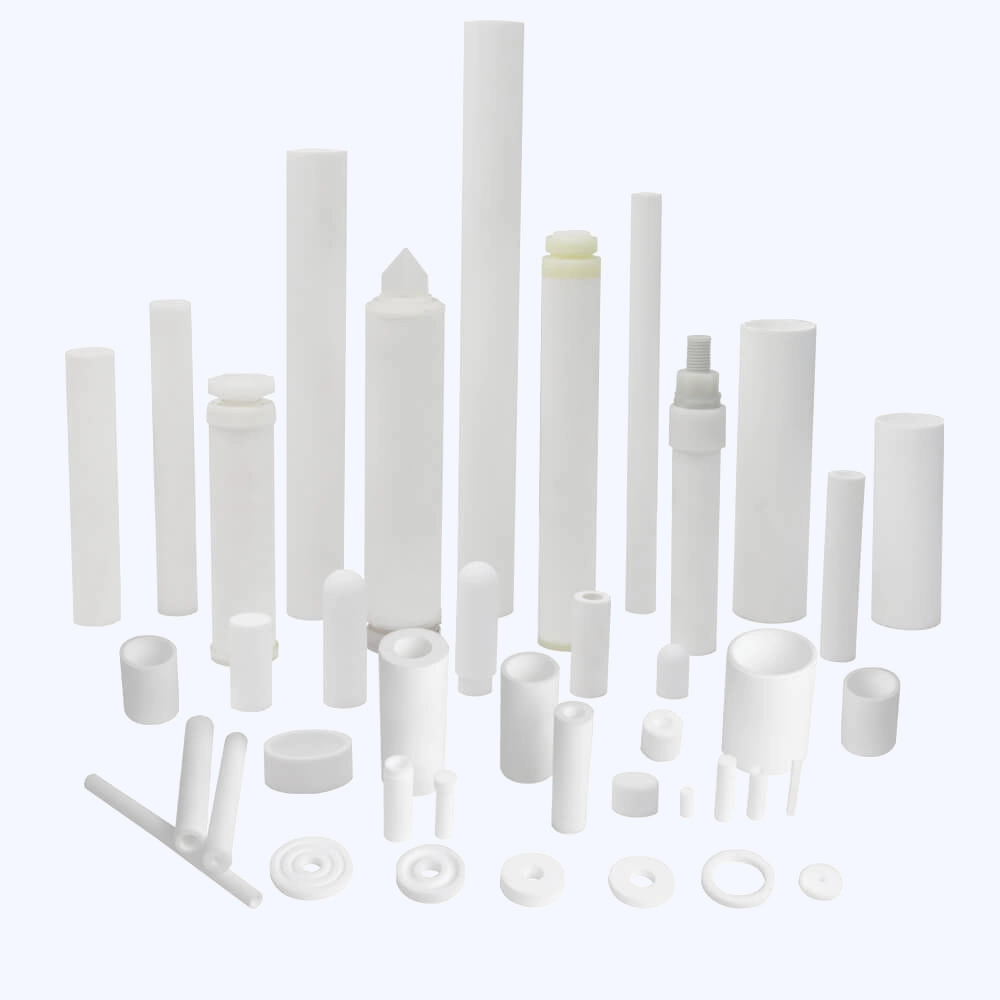
Parameters
• Technical parameters PP sintered products with uniform pore size distribution, good circulation, and large flux Resistant to strong acids and alkalis, salt, and most organic solvents.
• Easy to blow back, high regeneration efficiency, PP material product temperature resistance of 80 °C, filtration precision of 1 to 200 °C, non-toxic tastelessness, no media off, superior mechanical properties, not easy to damage the raw material in line with GMP and FDA requirements, no adhesive, and a wide range of chemical compatibility.
We’ve got answers.
Browse some answers to our most common questions, or you can drop us a line to ask something else.
Porous Plastic Filter
How do I clean and maintain sintered porous filter discs?
Cleaning methods depend on the material used. For metal discs, methods may include backwashing, ultrasonic cleaning, or chemical cleaning. Polyethylene discs are often cleaned with mild detergents. Regular maintenance ensures a prolonged operational life.
How to Calculate Filter Porosity?
Filter porosity is classified into three major types: Primary Porosity, Secondary Porosity, and Effective Porosity. The calculation involves determining the ratio of the volume of gaps in the filter to the total volume, expressed as a percentage.
Porosity = (Volume of Empty Gaps/Total Volume of Filter) x 100
Other methods include:
• Direct Methods: Calculate the entire volume of the porous filter and the volume of a skeletal filter (without pores) to find the porosity.
• Computed Methods: Use modern computer technology to obtain a 3D image of a porous filter and employ defect analysis techniques.
• Water Evaporation Technique: Calculate porosity by determining the difference in weight between the saturated filter in water and the dried filter.
What is Porosity in Filtration?
Porosity, in the context of filtration, measures the pores on the filter surface, determining its efficiency and capabilities. Higher porosity indicates more open structures (pores), allowing maximum flow with minimal pressure drops.
However, it's crucial to note that a higher porosity rate doesn't necessarily guarantee greater efficiency. When selecting the right material for your porous metal filter, consider aspects such as pore size, pressure drop, temperature resistance, and strength.
• Size of Pores: Micron rating is crucial. A material rated at 5 microns will likely stop particles of 5 microns or larger.
• Pressure Drop: Choose a material with a minimum pressure drop for uniform flow.
• Temperature Resistance: Analyze the material's capability to perform efficiently under specific temperatures.
• Strength: Opt for a filter with the strength to withstand changing environmental conditions.
How do I choose the right sintered porous filter disc for my application?
Consider factors such as the nature of the substances being filtered, operating conditions (temperature, pressure), chemical compatibility, and desired filtration precision. Consulting with filtration experts can help guide the selection process.
In what industries are sintered porous filter discs commonly used?
They are widely used in industries such as petrochemicals, pharmaceuticals, water treatment, food and beverage, automotive, and more, owing to their versatility and effective filtration capabilities.
What is a sintered plastic porous filter?
A sintered plastic porous filter is a filtration device made from polymeric materials that are compressed and heated to form a porous structure with controlled pore sizes and distribution.
Want to talk to us
Get in touch
Please fill in the form below. We aim to reply within 1 business day.
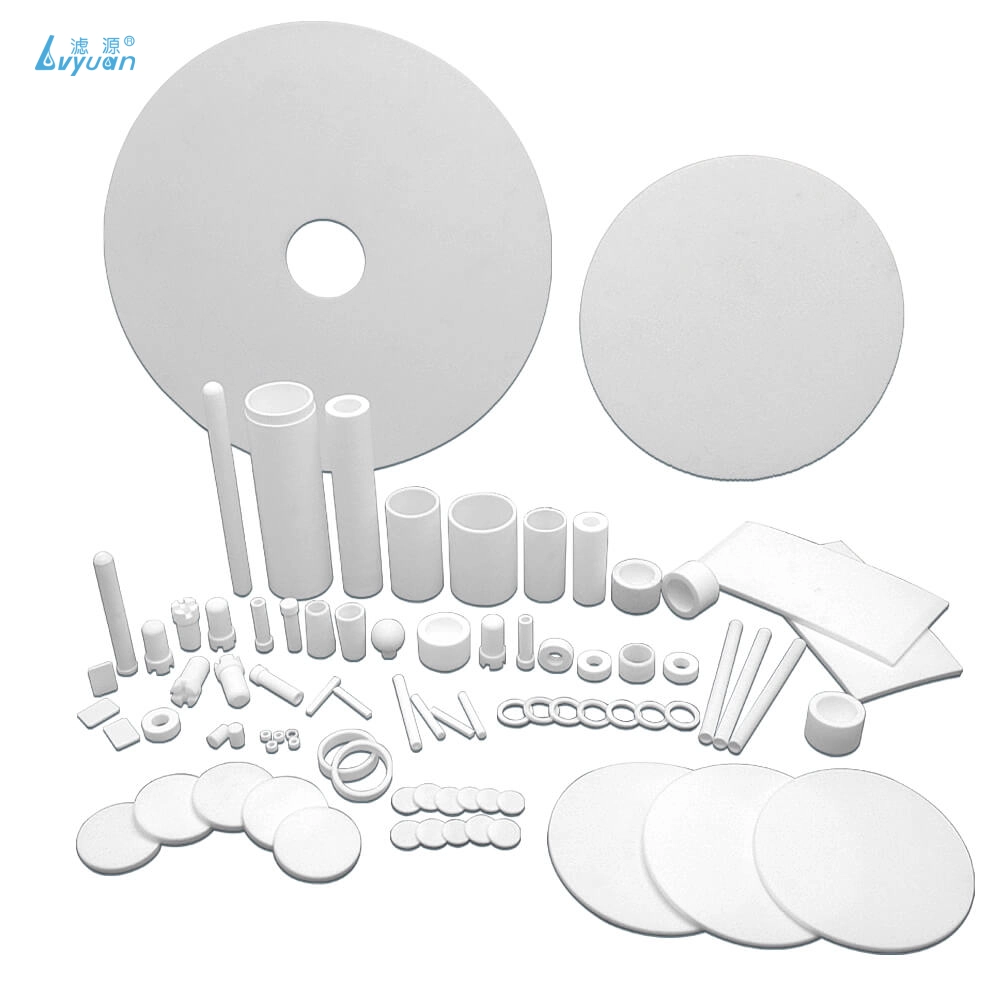
Sintered PE Filter
Lvyuan Sintered polyethylene PE pipe or plate can be used for vacuum filtration, pressure filtration or gravity filtration.
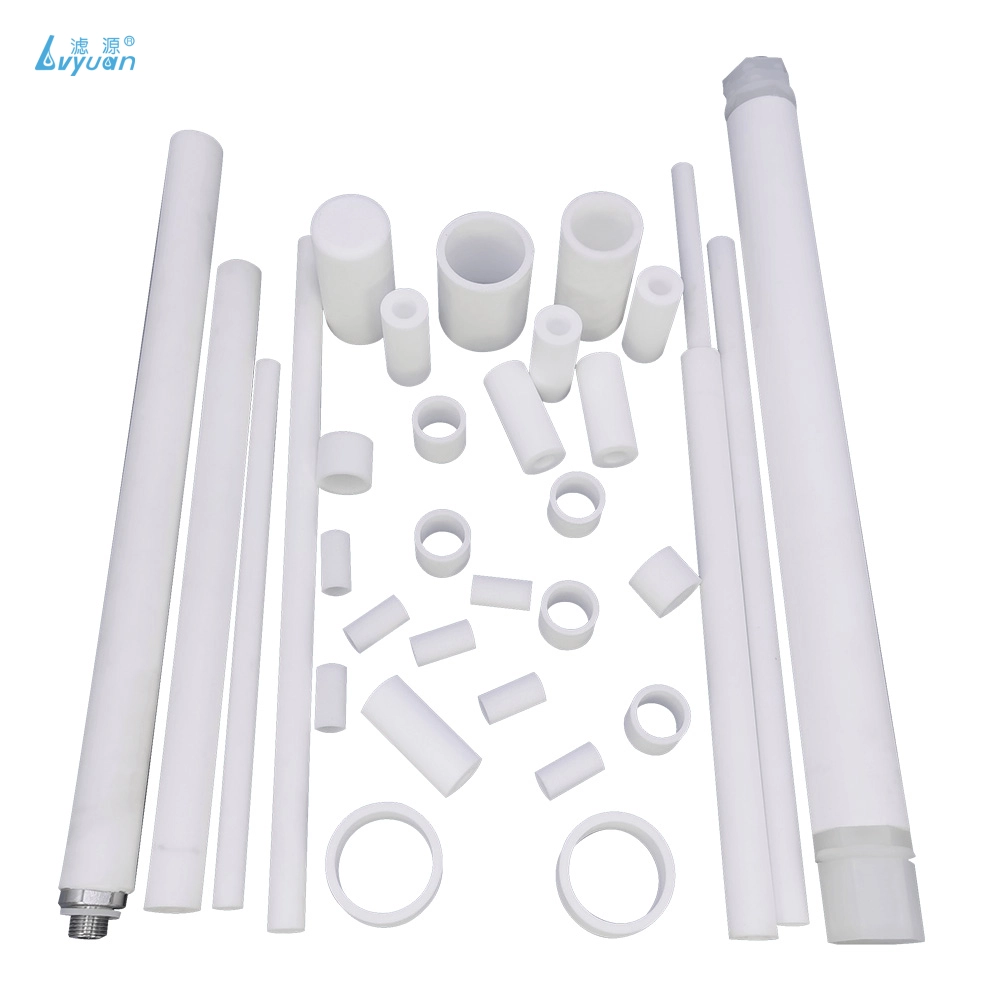
Sintered PTFE Filter
The sintered PTFE filter is a high-performance filtration solution designed to effectively remove impurities and contaminants from fluids, offering exceptional chemical resistance and durability in various industrial applications.
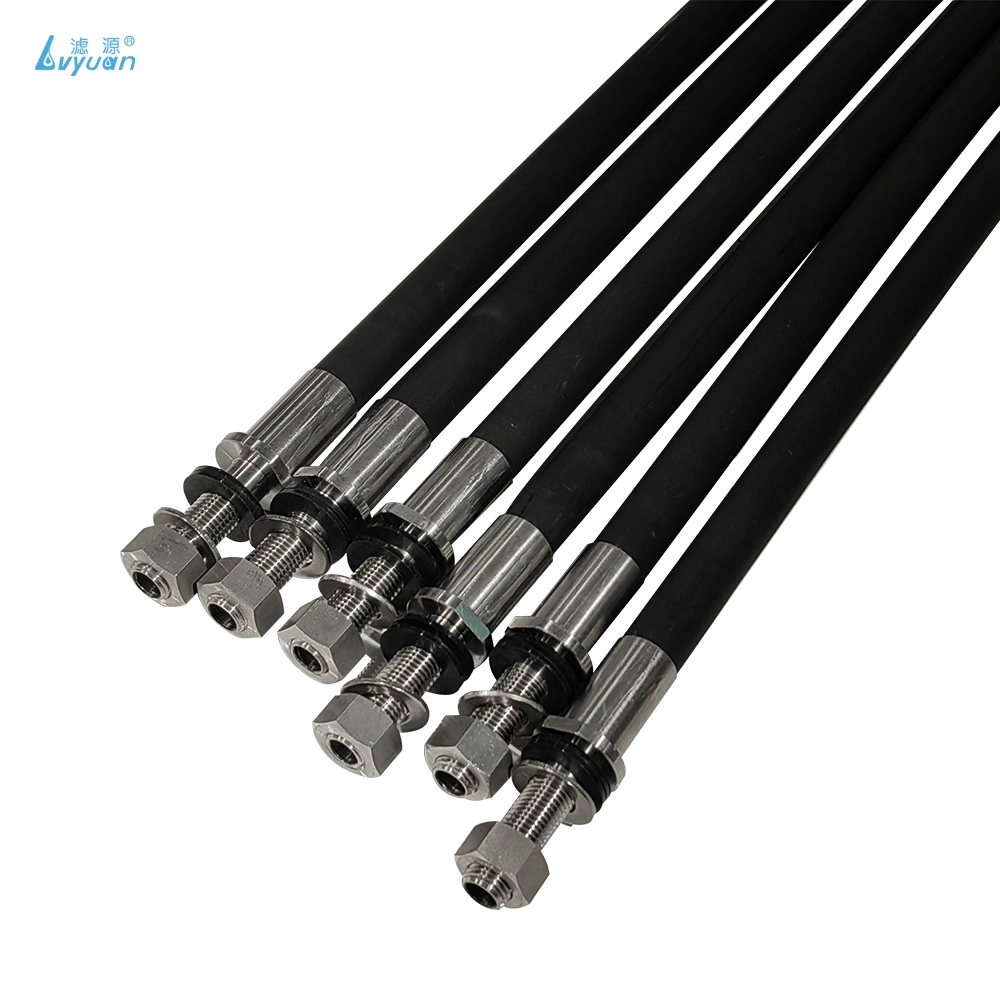
PA Filter
Sintered PA filter cartridge is made of high quality polymer polyethylene as the main raw material and carbon fiber sintered by scientific formula. It is compact, sturdy, light and can withstand high pressure, non-toxic and tasteless, and has good corrosion resistance to acid and alkali.
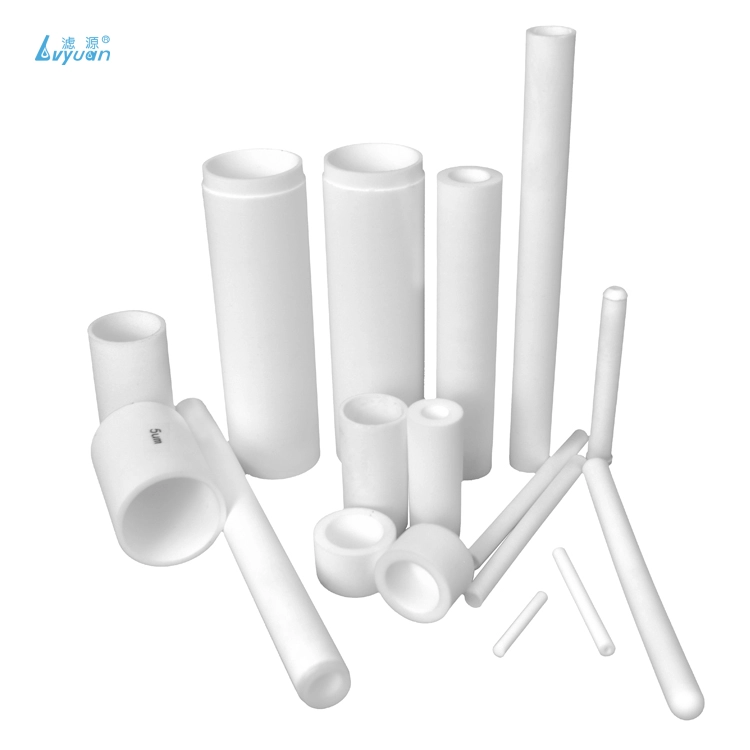
Sintered PP Filter
High-quality polypropylene(PP) is used as the main raw material and sintered by scientific formula, which is compact, strong, light and can withstand high filtration pressure, and the aperture of the cartridge is the same inside and outside, so it is easy to blow back and de-flow, and has good corrosion resistance to acid and broken solvent.
© 2024 Lvyuan All Rights Reserved. | Privacy policy • Terms and conditions