Exploring Disadvantages of Sintering | Lvyuan
What are the Disadvantages of Sintering?
Sintering, a process widely used in various industries to create solid materials from powders, offers numerous advantages such as enhanced mechanical properties and material density. However, like any manufacturing process, it comes with its set of drawbacks. This article delves deep into the disadvantages of sintering, offering insights into the challenges faced by industries, including companies such as Lvyuan, a leading industry filter manufacturer based in China.
Understanding Sintering and Its Applications
Before exploring the disadvantages, it's important to understand what sintering entails. Sintering involves heating powder materials below their melting point until particles adhere to each other. This method is commonly used in the production of ceramics, metals, and plastics, and it plays a crucial role in the fabrication of high-performance components in industries such as automotive, aerospace, and filtration systems.
Disadvantages of Sintering
Despite its wide range of applications, sintering is not without its limitations. Here are some key disadvantages associated with this process:
1. High Production Costs
Sintering can be expensive due to the high cost of equipment and energy requirements. The process demands precise control of atmospheric conditions and temperatures, often necessitating sophisticated machinery and technology that can strain budgets, especially for large-scale production.
2. Energy Consumption
The sintering process is energy-intensive, contributing to higher operational costs and impacting environmental sustainability. The requirement for sustained high temperatures leads to significant energy consumption, making it a less eco-friendly option compared to alternative methods.
3. Limited Material Scope
Not all materials are suitable for sintering. Some compounds cannot withstand the thermal stresses involved, limiting the range of materials that can be effectively processed through this method. This limitation necessitates the exploration of alternative processes for specific materials.
4. Long Processing Time
Sintering is not a quick process. Depending on the material and required properties, it can be time-consuming, with some processes taking several hours to complete. This can reduce production efficiency and lead to longer lead times, impacting overall throughput.
5. Potential for Structural Inhomogeneities
The sintering process can sometimes result in uneven density and structural inhomogeneities within the material. These inconsistencies can affect the mechanical properties of the finished product, potentially compromising performance and quality.
Lvyuan's Take on Sintering Challenges
As a leading sintered filter manufacturer, Lvyuan recognizes these challenges and has actively worked to mitigate them. Our expertise in designing and manufacturing top-notch sintered filters and filter housings pushes us to constantly explore innovative solutions to enhance quality and efficiency while minimizing inherent disadvantages.
Technological Advancements and Lvyuan's Approach
Despite the drawbacks, advancements in technology provide avenues to address these issues. Lvyuan focuses on integrating state-of-the-art technologies and continuous process improvements to optimize energy use, reduce production time, and enhance material properties. Our commitment to innovation ensures that we stay at the forefront of providing high-quality filtration solutions.
Conclusion
Understanding the disadvantages of sintering allows industries to make informed decisions when adopting this technology. While it presents challenges such as high costs and energy consumption, the ongoing advancements in the field and the expertise of companies like Lvyuan pave the way for solutions that mitigate these drawbacks, ensuring the continued viability and enhancement of sintering in modern manufacturing.
Frequently Asked Questions
1. What materials are best suited for sintering?
Materials with high melting points and those that can handle thermal stresses, such as metals and ceramics, are best suited for sintering. However, not all materials can benefit due to the limitations mentioned.
2. How does Lvyuan address the disadvantages of sintering?
Lvyuan employs advanced technology and process improvements to reduce energy consumption, enhance material properties, and maintain production cost-effectiveness, ensuring high-quality sintered filters.
3. Are there newer methods that reduce the energy consumption of sintering?
Yes, advancements such as spark plasma sintering and selective laser sintering are being researched and implemented to lower energy consumption and enhance efficiency.
By exploring and understanding the disadvantages of sintering, industries can better equip themselves to leverage this technology effectively, adapting innovative solutions like those offered by Lvyuan to overcome challenges and drive success in manufacturing.
How to Clean Sintered Metal Filter: Step-by-Step Guide | Lvyuan
Custom titanium rod filter cartridge Manufacturers and suppliers
Custom sintered powder metal filter cartridge Manufacturers and suppliers
How Long is the Life of Sintered Metal Filters? - Lvyuan
Sintered Powder Filters
What is a sintered powder filter?
A sintered powder filter is a porous filtration medium created by compacting and sintering metal powders. It is designed to provide efficient and precise filtration in various industrial applications.
For products
What applications are suitable for sintered metal filters?
Sintered metal filters are versatile and find applications in various industries such as pharmaceuticals, petrochemicals, food and beverage, water treatment, and more. They are commonly used for gas and liquid filtration.
Metal mesh filters
Can sintered wire mesh filter be customized?
Yes, sintered wire mesh can be customized in terms of material, pore size, thickness, and dimensions to suit specific filtration requirements. Customization allows for optimal performance in diverse applications.
Sintered mesh filters
How does a sintered mesh filter work?
Sintered mesh filters work by trapping and retaining particles within the porous structure of the mesh. The sintering process fuses the mesh layers, creating a robust filter with uniform openings that allow controlled passage of fluids while capturing contaminants.
Stainless Steel Pleated Filter Cartridges
What is a Stainless Steel Pleated Filter Cartridge?
A Stainless Steel Pleated Filter Cartridge is a filtration device with a pleated design, made from high-quality stainless steel (SS 304 or SS 316L). It is used for efficient particle removal in various industrial applications.
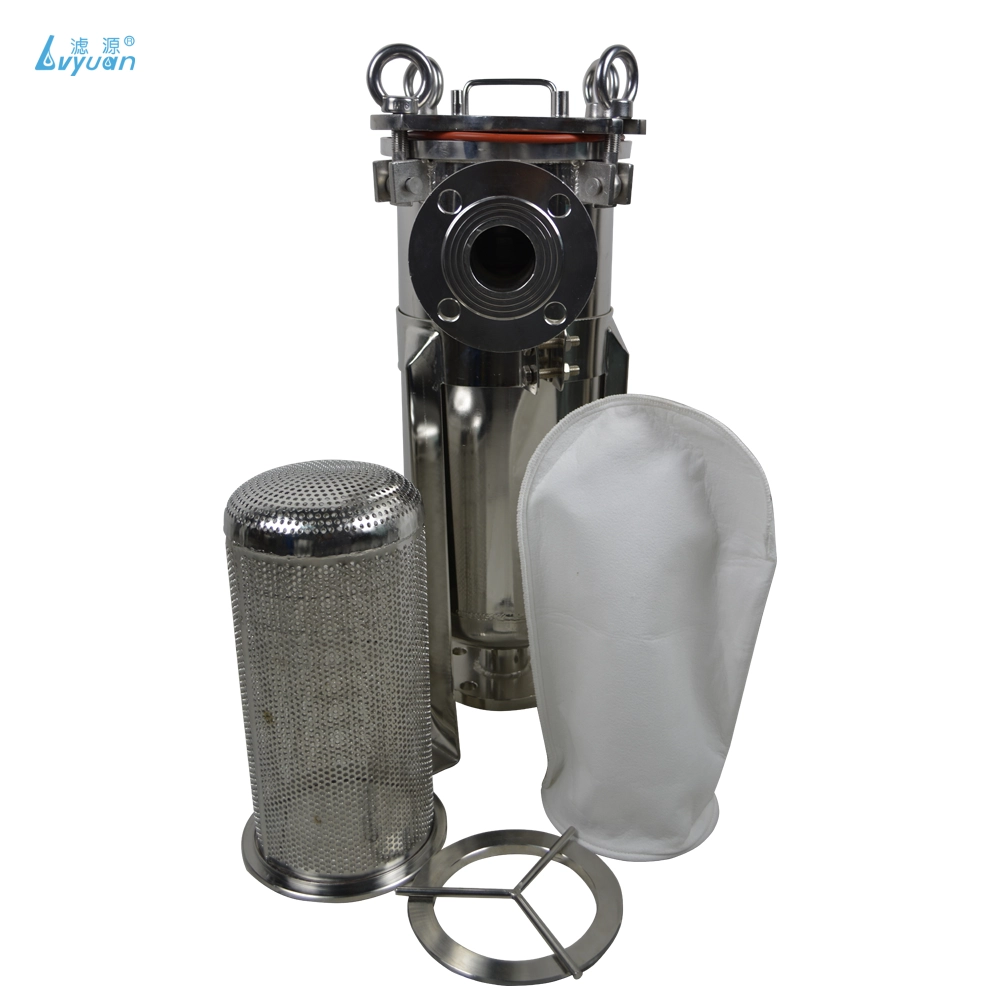
Bag filter housing
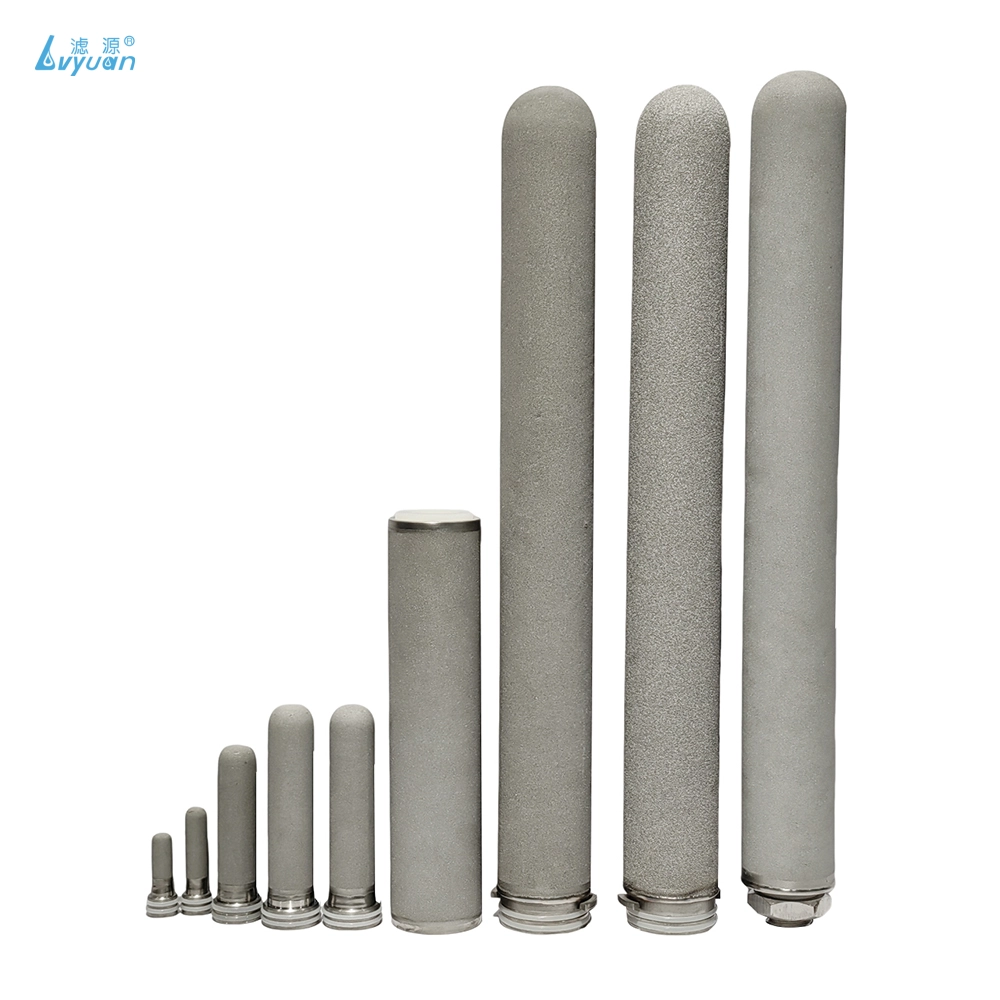
Sintered powder metal filters
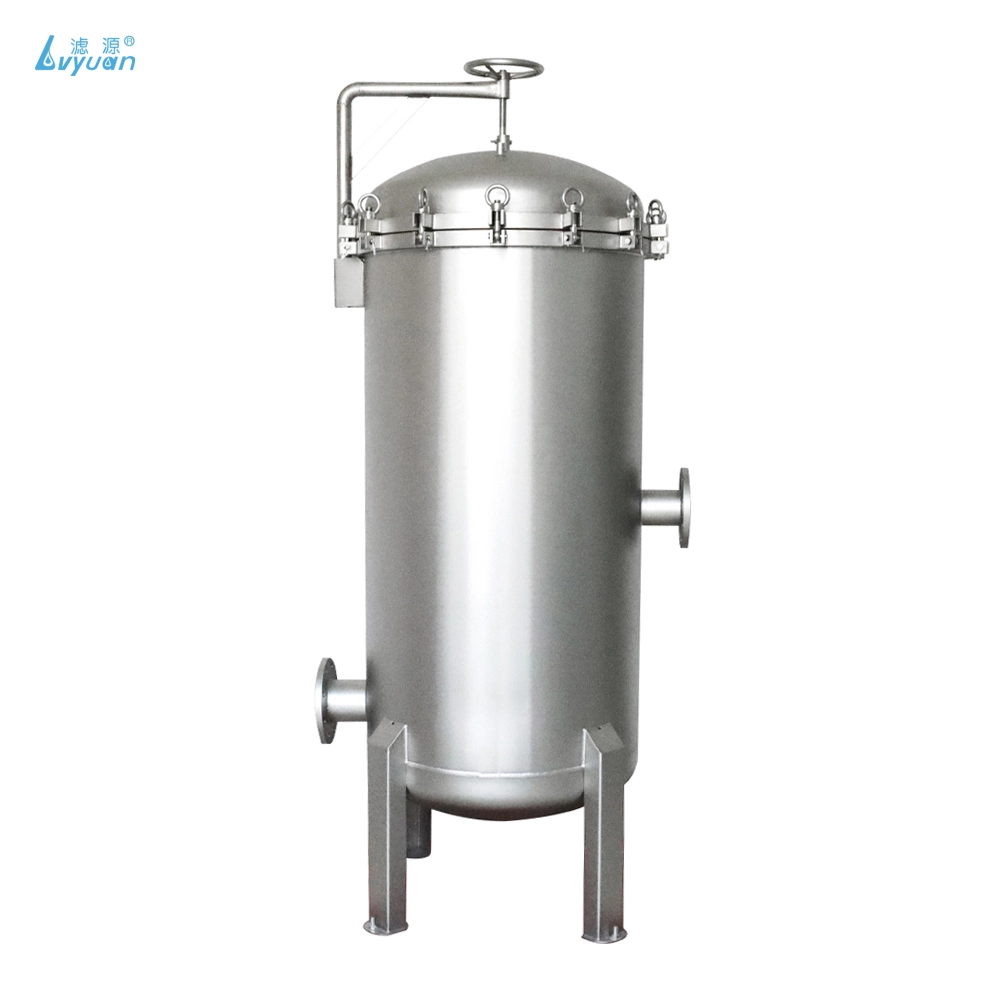
Stainless steel multi cartridge filter housing
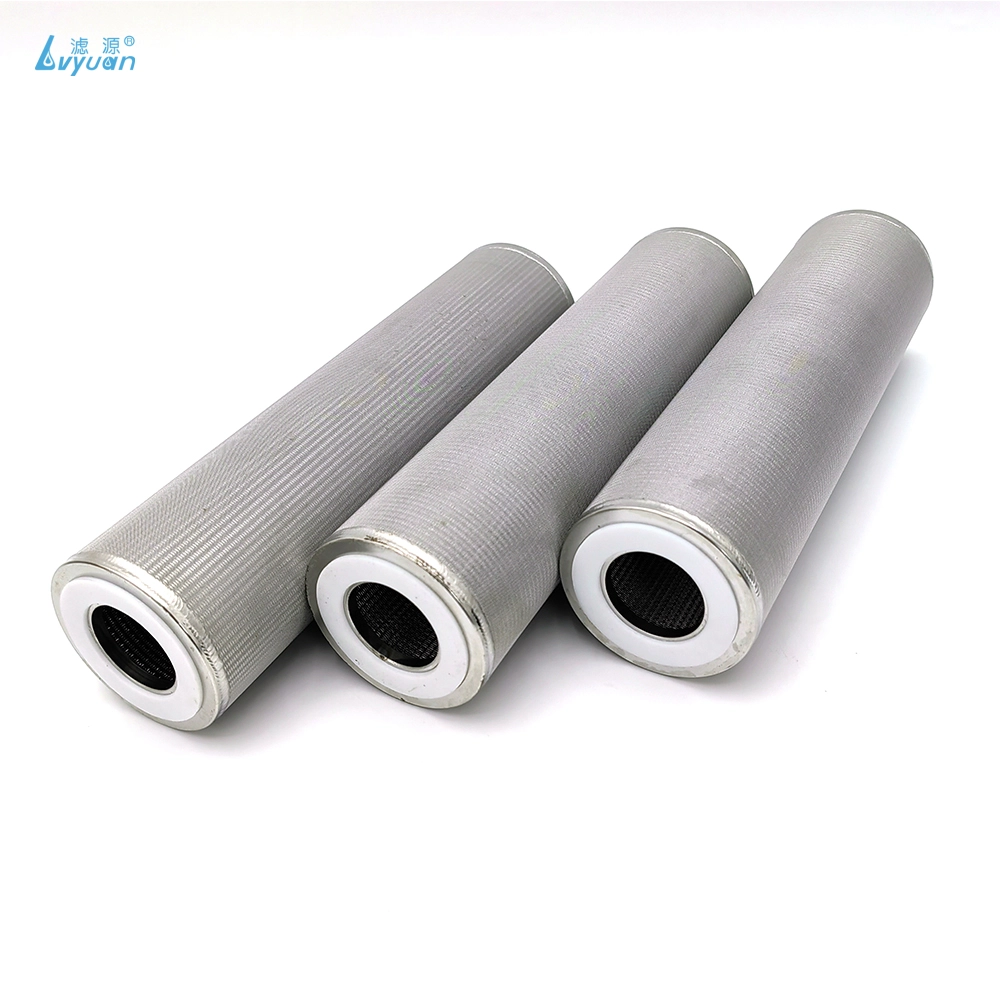
Sintered wire mesh filter
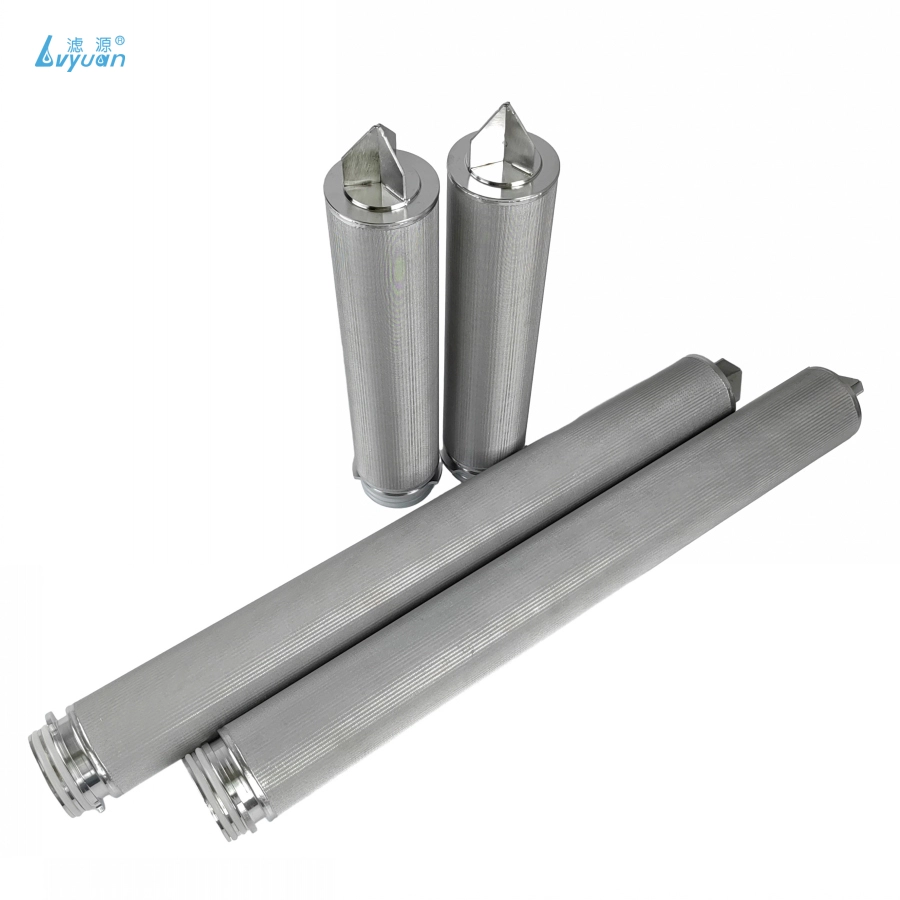
stainless steel filter water
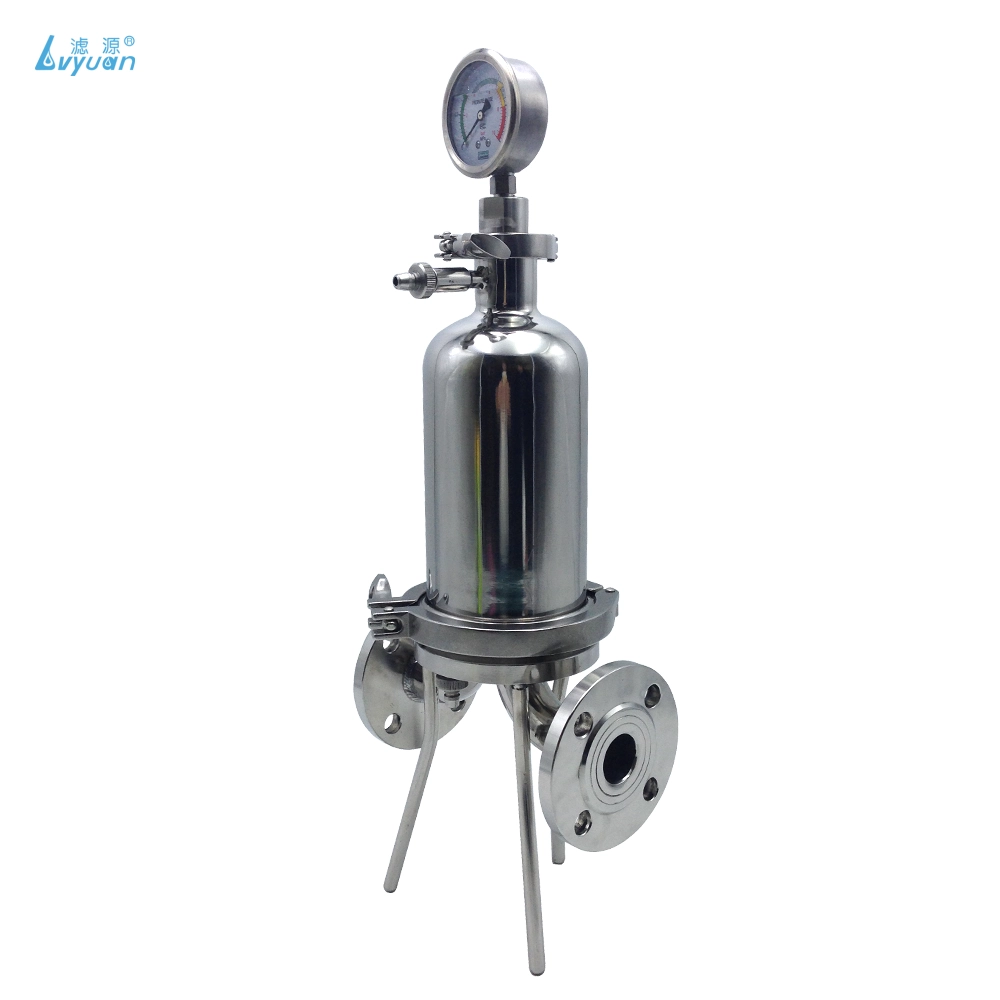
Sanitary filter housing
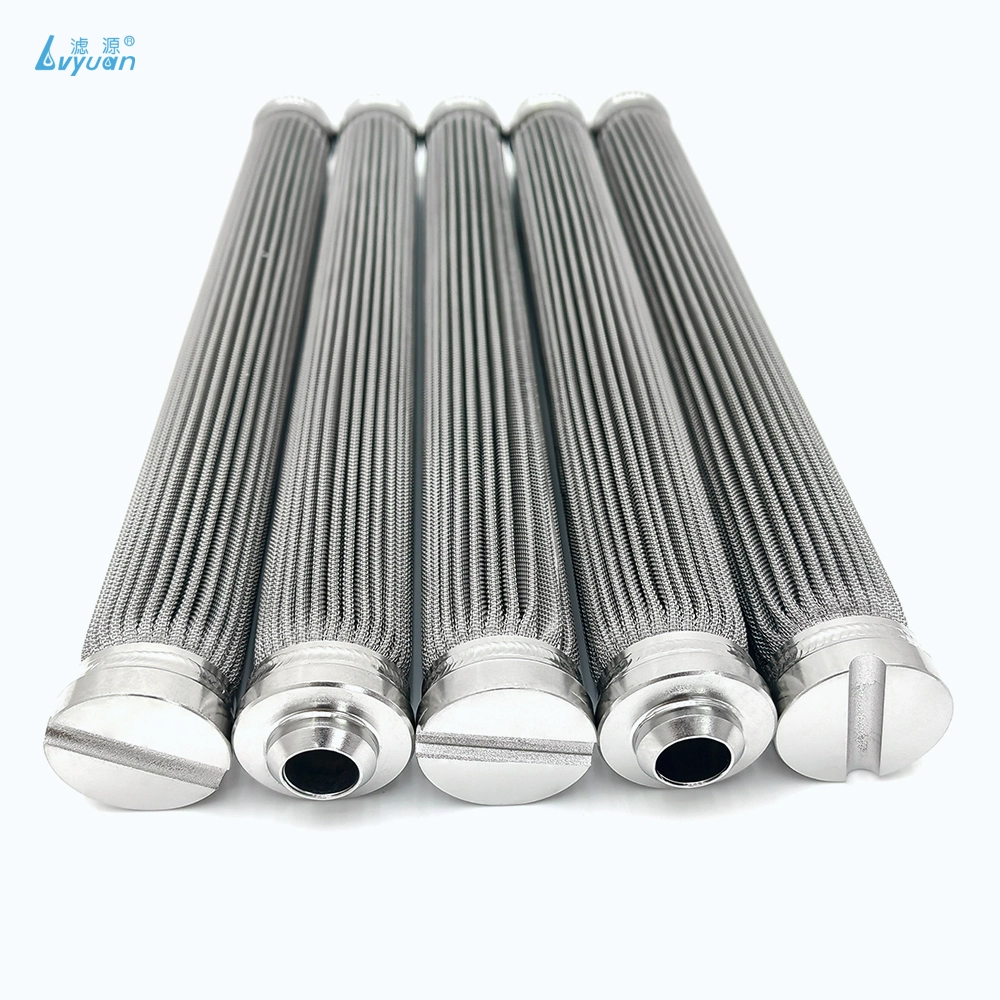
Stainless steel pleated filter cartridge
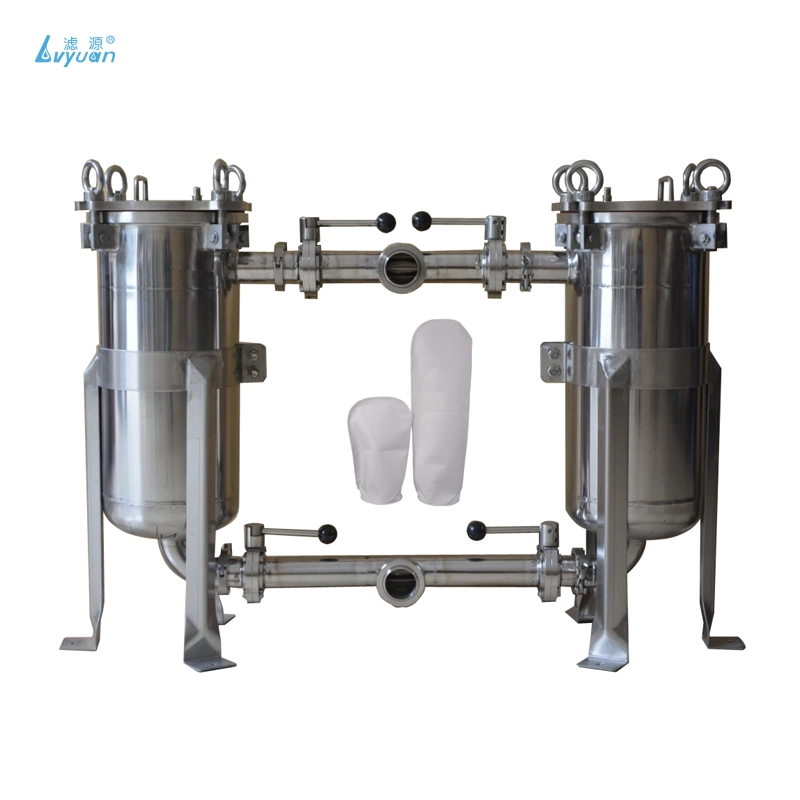
Stainless Steel Duplex filter housing
© 2024 Lvyuan All Rights Reserved. | Privacy policy • Terms and conditions