Sintered Filter Element Manufacturing Process and Applications
Discover the intricate Sintered Filter Element Manufacturing Process and its diverse applications with Lvyuan. Our expertly crafted filtration solutions ensure high performance and reliability across various industries. Dive into the world of precision-engineered filters designed to optimize your operations.
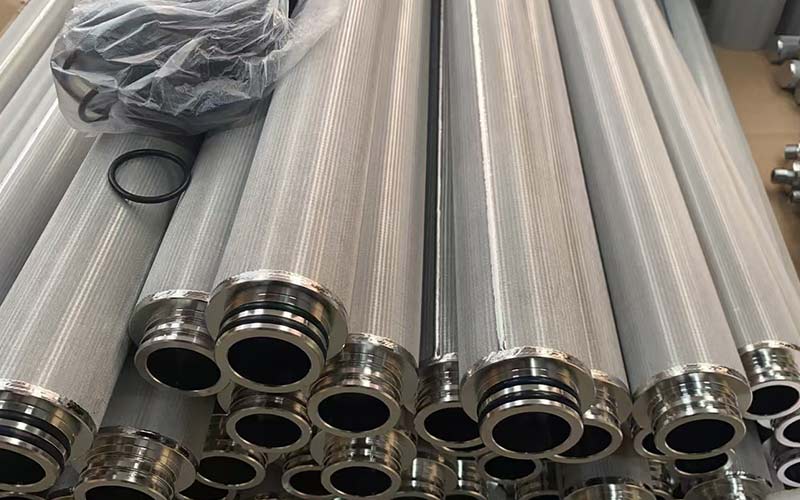
-
Introduction
Sintered filter elements, made from materials like stainless steel and nickel-based alloys, are designed to meet the demanding requirements of high-temperature environments and precise filtration needs. These filters offer high strength, excellent thermal stability, and ease of cleaning, making them ideal for applications such as gas distribution, high-precision filtration, and high-pressure backwash oil filters in industries like petroleum and petrochemicals. In this blog, we’ll explore the manufacturing process, key features, and diverse applications of sintered filter elements.
1. Sintered Filter Element Manufacturing Process
The manufacturing of sintered filter elements involves several critical steps to ensure their high performance and durability. The process is both precise and sophisticated, as it combines different materials and advanced techniques to create filters capable of withstanding extreme conditions.
·Material Preparation
The first step in the sintered filter element production process is selecting the right materials. Stainless steel is the most commonly used material, but other metals like nickel-based alloys can also be employed, depending on the intended application. These materials are chosen for their ability to withstand high temperatures, mechanical stress, and corrosion.
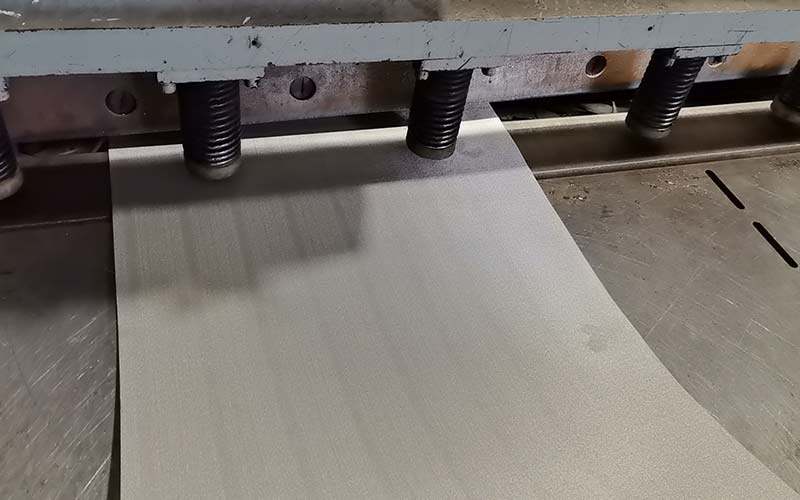
·Layered Stamping
In this stage, multiple layers of metal mesh are stacked and pressed together under high pressure. This step forms a pre-shaped filter element that will later undergo sintering. The layers of mesh are aligned in a way that ensures uniform filtration and structural integrity.
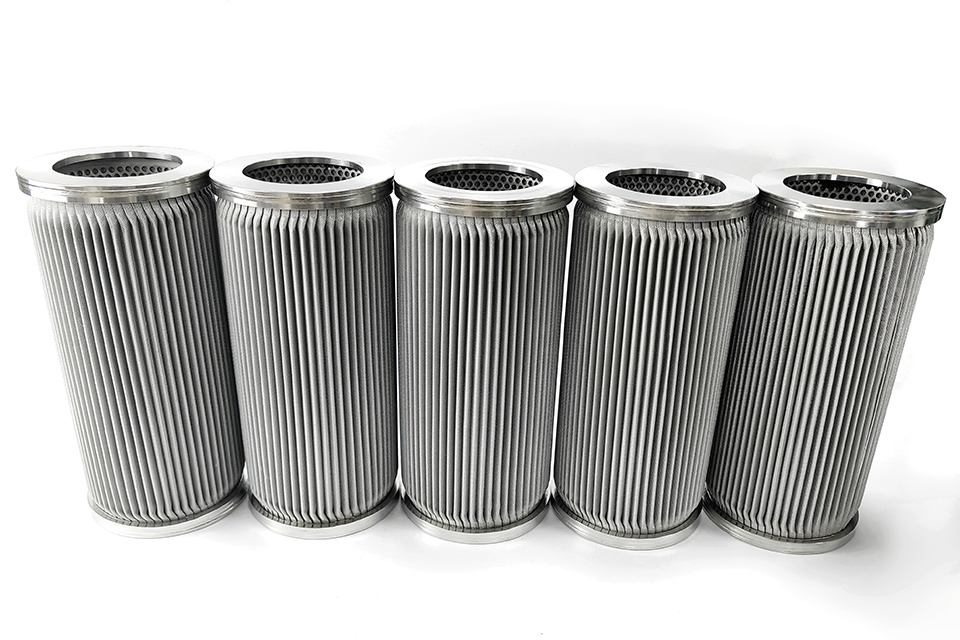
·Vacuum Sintering
The pre-formed mesh structure is then placed in a vacuum furnace where it undergoes high-temperature sintering. This process causes the metal layers to bond together at their points of contact, ensuring that the filter element has uniform and precise pore structures. The sintering process also enhances the filter's strength and durability, ensuring that it can handle high pressures and extreme temperatures.
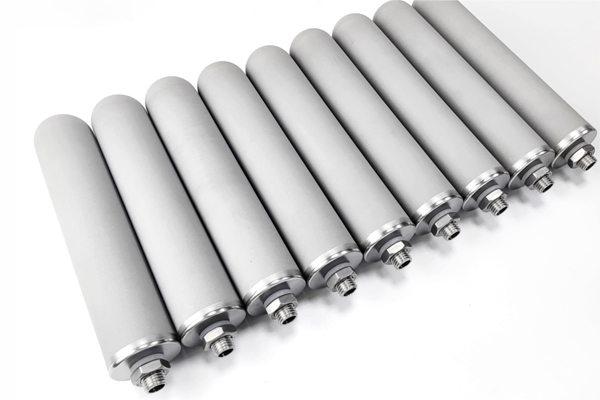
2. Key Features of Sintered Filter Elements
Sintered filters are known for their remarkable properties, which make them suitable for demanding industrial applications. Some of the most notable features include:
High Strength
After sintering, the filter elements exhibit exceptional mechanical strength and pressure resistance. This makes them ideal for use in high-pressure filtration systems, where other filter types might fail.
High Precision
Sintered filters can offer precise filtration capabilities, with particle filtration sizes ranging from 2 to 200 microns. They ensure consistent filtration performance, making them suitable for applications requiring high levels of purity.
Thermal Stability
One of the standout features of sintered filter elements is their ability to operate in a wide temperature range. These filters can function effectively from temperatures as low as -200°C to as high as 650°C, allowing them to be used in a variety of extreme environments.
Cleanability
Sintered filter elements have a surface filtration structure that enables easy backflushing or reverse flow cleaning. This feature ensures that the filter remains functional over time, reducing maintenance needs and extending its operational life.
3. Applications of Sintered Filter Elements
The unique properties of sintered filter elements make them highly versatile, and they are used in several key industrial applications:
High-Temperature Environments
Sintered filters are ideal for use in high-temperature environments, such as in heat exchangers or cooling systems, where other materials may degrade. They provide effective filtration while enduring extreme temperatures.
Gas Distribution
These filters are often used in gas distribution systems, particularly in applications involving fluidized beds or other high-temperature gas processes. They help distribute gases evenly while removing impurities that may affect system efficiency.
High-Precision Filtration
Sintered filter elements are commonly used for high-precision filtration in critical industries such as pharmaceuticals, food processing, and petrochemical manufacturing. Their ability to filter particles as small as 2 microns ensures that products meet stringent quality standards.
High-Pressure Backwash Oil Filters
In the petroleum and petrochemical industries, sintered filter elements are used in high-pressure backwash oil filters. These filters help separate oil from process fluids, ensuring that equipment runs smoothly and product quality is maintained. Their resistance to pressure and heat makes them ideal for such demanding applications.
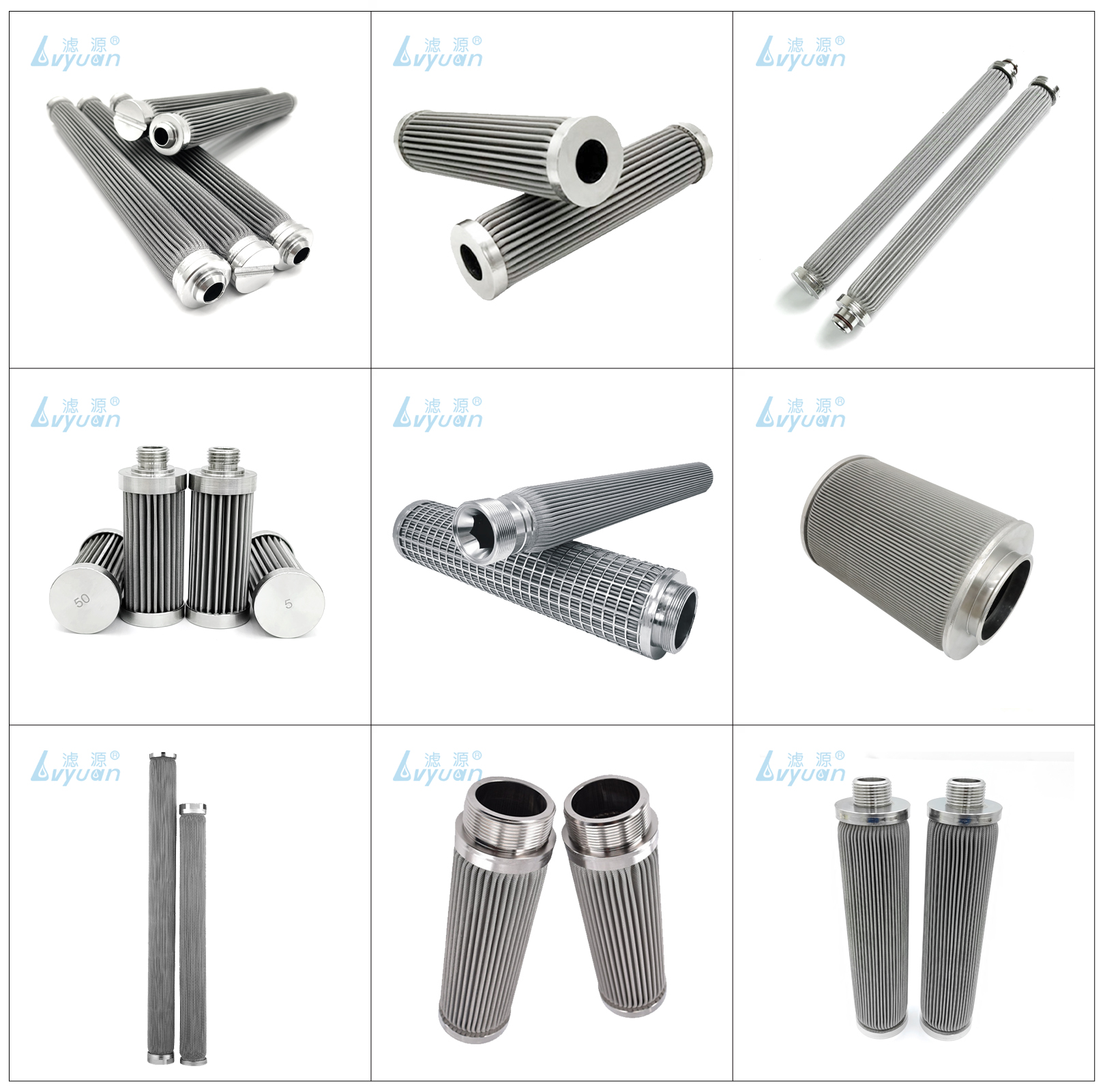
Conclusion
Sintered filter elements are an excellent solution for industries requiring robust, high-precision filtration. The manufacturing process, which combines materials like stainless steel and nickel-based alloys with advanced techniques such as vacuum sintering, results in filters that are strong, thermally stable, and highly effective at removing fine particles.
From high-temperature environments to high-precision applications in petroleum and petrochemical industries, sintered filters provide unmatched durability and filtration accuracy. Their ease of cleaning and ability to handle extreme pressures and temperatures make them indispensable in many industrial settings.
FAQs
1.What materials are commonly used to make sintered filter elements?
Stainless steel is the most common material used, but nickel-based alloys and other metals are also used for specific applications requiring enhanced heat and corrosion resistance.
2. What filtration precision can sintered filters achieve?
Sintered filter elements can filter particles from 2 microns to 200 microns, offering high precision for various industrial applications.
3. Can sintered filters be cleaned and reused?
Yes, sintered filters are designed for easy cleaning, often using reverse flow or backwashing methods, making them reusable and cost-effective.
4. What industries benefit most from sintered filter elements?
Industries such as petroleum, petrochemicals, pharmaceuticals, food processing, and high-temperature engineering benefit from the strength and precision of sintered filters.
5. What are the temperature limits for sintered filter elements?
Sintered filter elements can operate effectively in a temperature range from -200°C to 650°C, making them suitable for extreme environments.
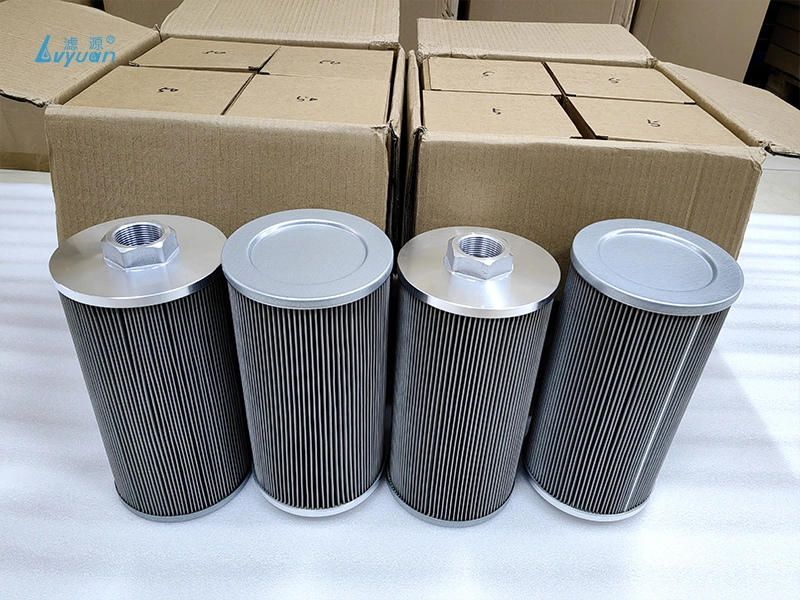
What is Sintered Metal Filter? Complete Guide by Lvyuan
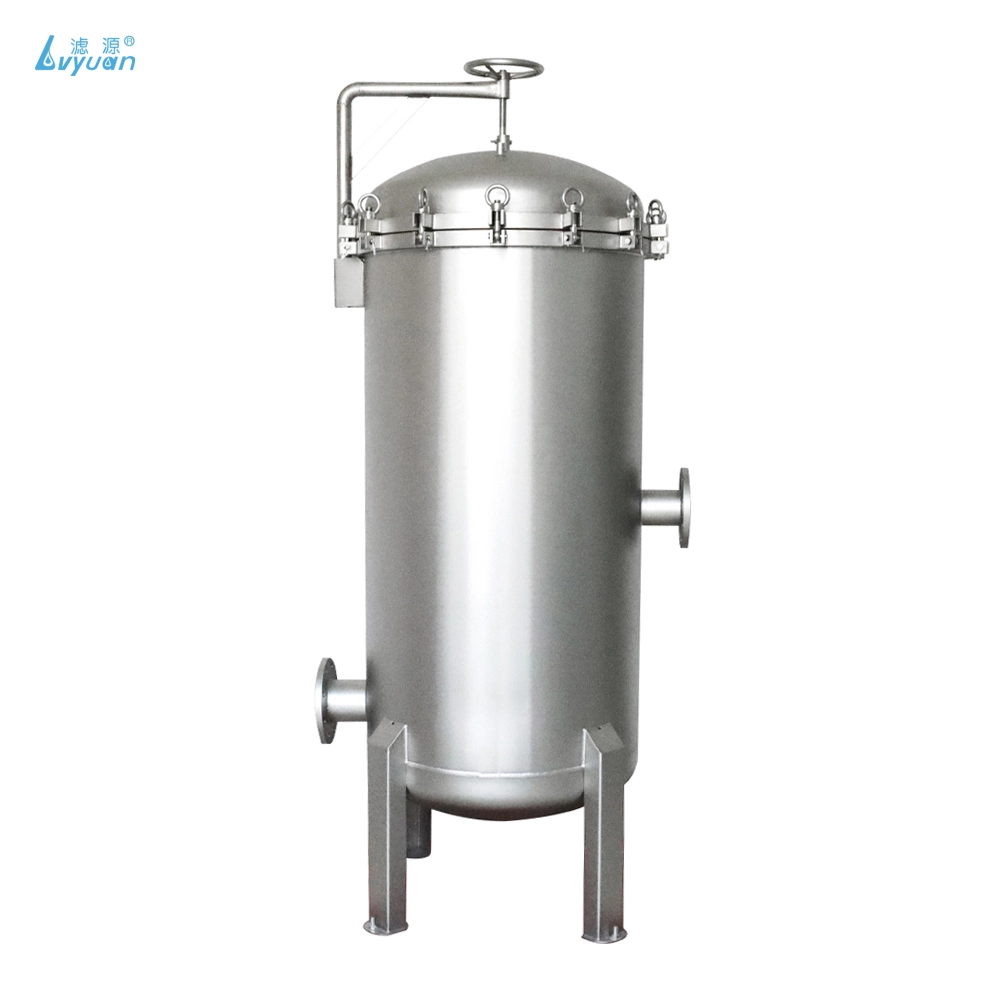
Applications of Sintered Metal Filters in Manufacturing
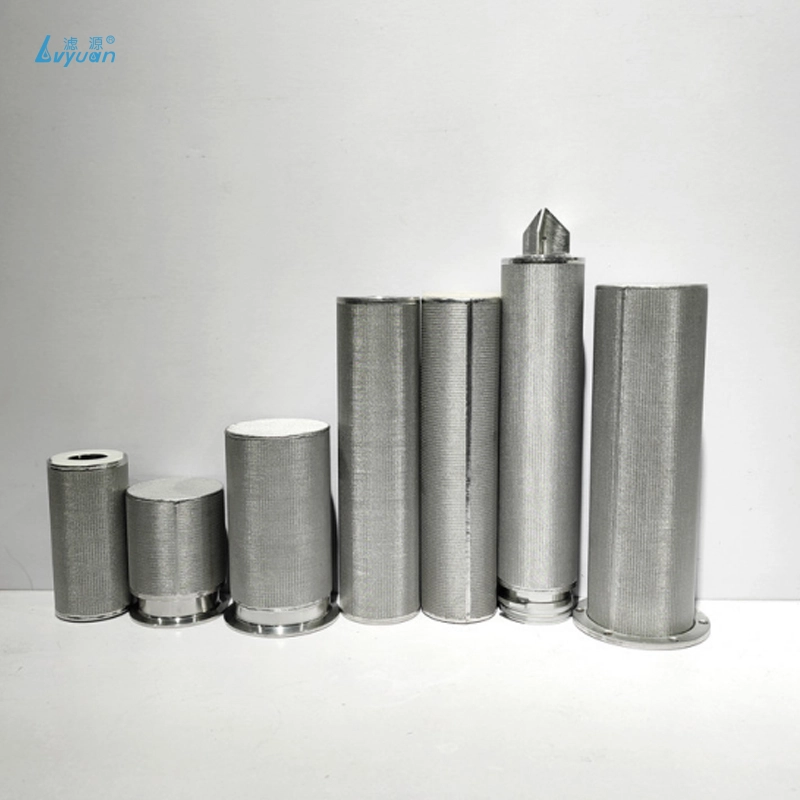
Why Lvyuan Is the Best China Manufacturer of Sintered Metal Filters
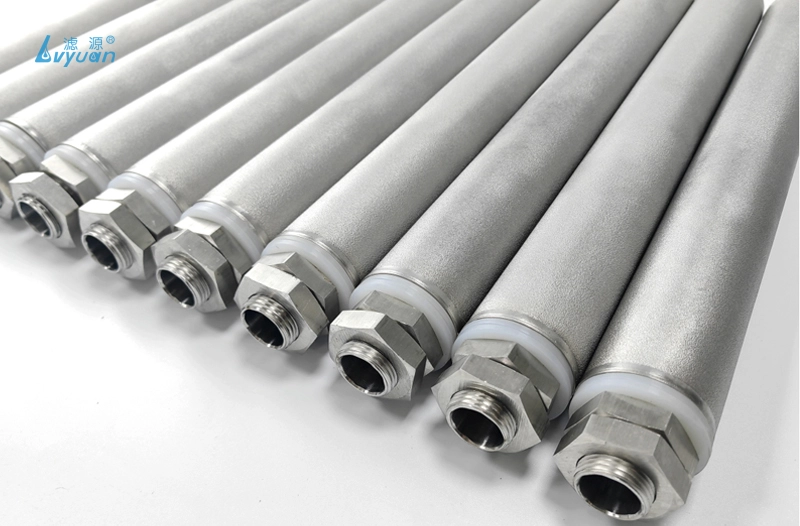
How to Clean Sintered Metal Filters: A Comprehensive Guide
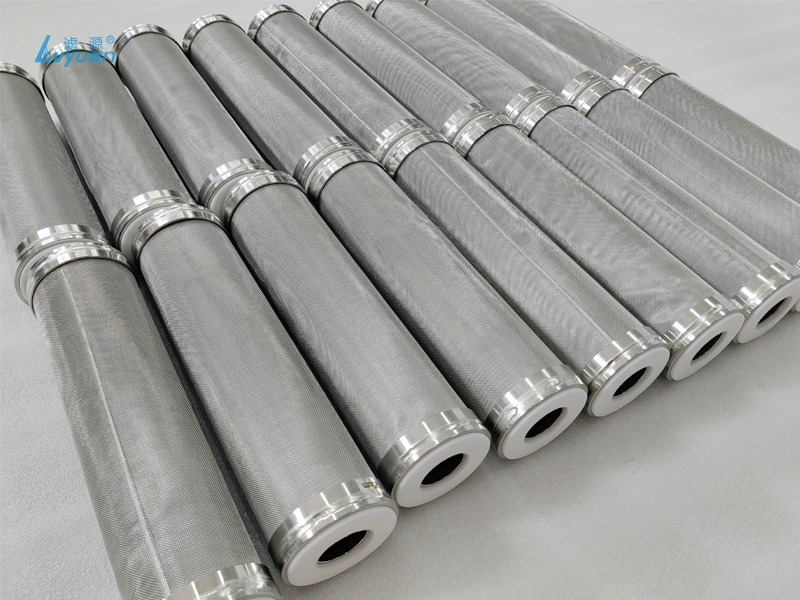
A Comprehensive Guide to Sintered Filters: Features, Production, and Benefits
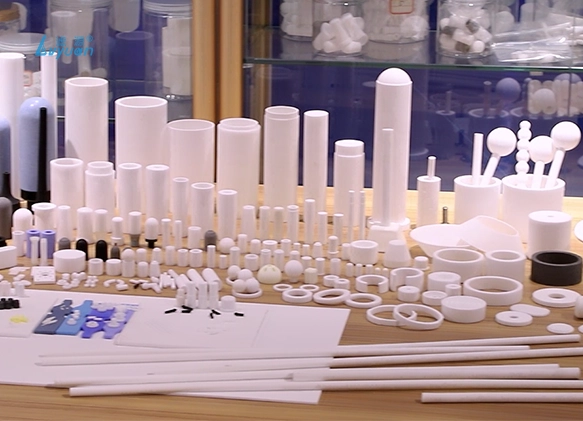
Sintered Plastic Filters: A Comprehensive Guide
Sintered Titanium Filters
What Micron Ratings Are Available for Sintered Titanium Filters?
Sintered titanium filters are available in a wide range of micron ratings and configurations, offering tailored solutions for optimal performance across diverse applications.
Sintered Metal Filters
What is a sintered metal filters?
A sintered metal filter is a porous material produced by compacting and heating metal particles to create a solid structure with interconnected pores. It is commonly used for filtration in various industries.
Metal mesh filters
What applications is sintered wire mesh suitable for?
Sintered wire mesh filter finds applications in various industries, including:
• Filtration of liquids and gases.
• Polymer and chemical processing.
• Pharmaceutical and food processing.
• Aerospace and automotive industries.
• Environmental protection and water treatment.
What types of contaminants can sintered wire mesh filter?
Sintered wire mesh can filter a wide range of contaminants, including particles, solids, and impurities from liquids and gases. The filtration efficiency depends on factors such as pore size and material selection.
Sintered mesh filters
How can I select the right sintered mesh filter for my application?
To select the right sintered mesh filter, consider factors such as filtration requirements, material compatibility, temperature and pressure conditions, and specific application needs. Consult with the manufacturer for guidance on customization options.
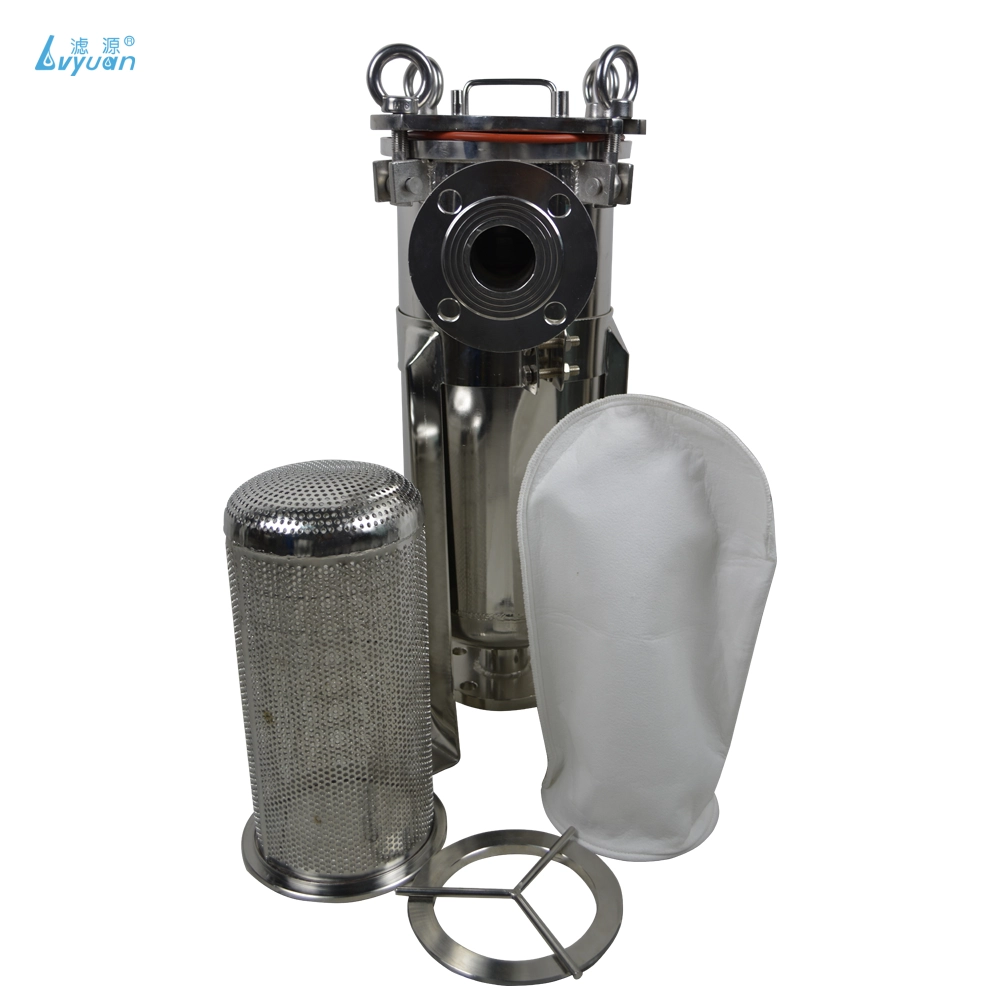
Bag filter housing
Bag filter housings are essential components in industrial filtration systems, designed to remove contaminants from liquids. To enhance the functionality and efficiency of bag filter housings, various features can be incorporated.
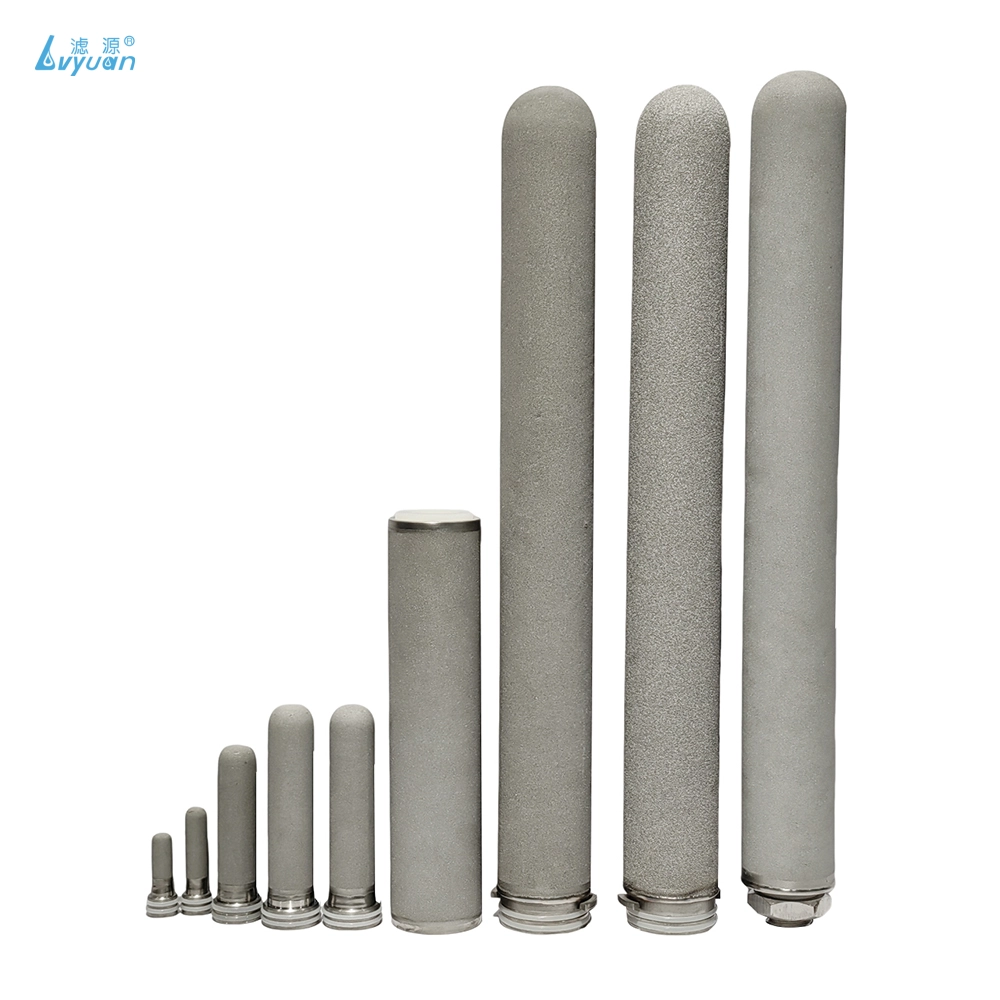
Sintered powder metal filters
Sintered powder metal filters are crafted from compressed and sintered metal powders, forming a porous structure. Porosity: 28%-50% Permeability: 0.02-20L/cm²minPa Pressure Resistance: 0.5Mpa Temperature Resistance: Less than 280℃
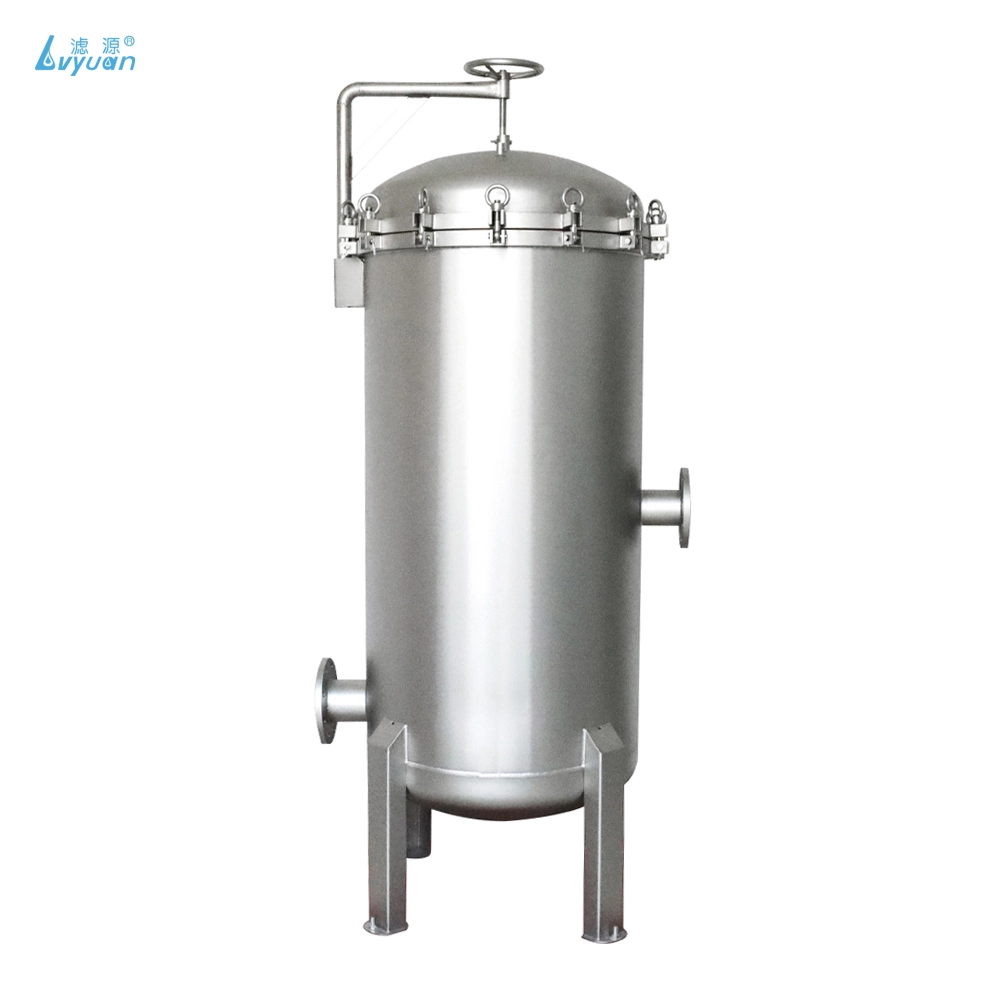
Stainless steel multi cartridge filter housing
Discover unparalleled filtration efficiency with our Stainless Steel Multi Cartridge Filter Housing – a testament to precision engineering and reliability.
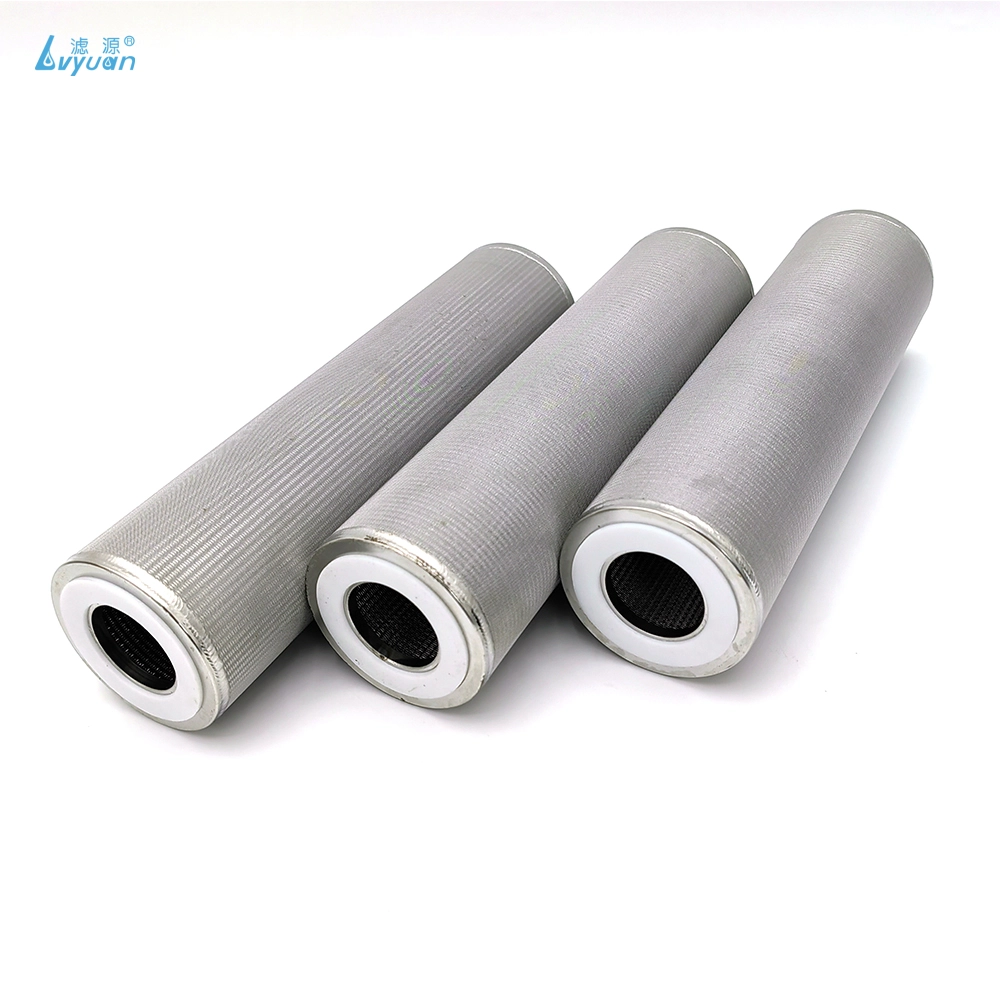
Sintered wire mesh filter
Benefit from outstanding high-pressure resistance and consistent filtration efficiency with Lvyuan's sintered metal mesh. Our sintered wire mesh finds versatile applications in diffuser screens, centrifuges, breather vents, fluidized beds, chromatography, polymer processing, petrochemical industries, hydraulic filters, and more.
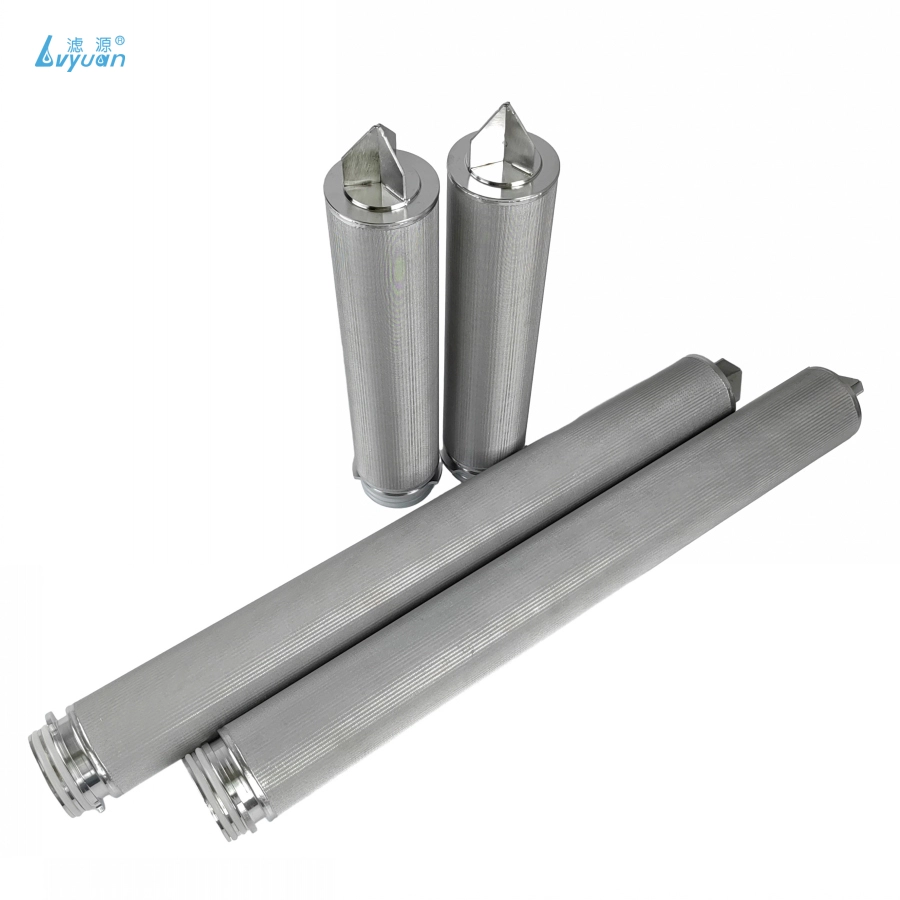
stainless steel filter water
Lvyuan’s sintered stainless steel filter stands as a pivotal filtration element crafted through a meticulous sintering process, with stainless steel serving as the core material.
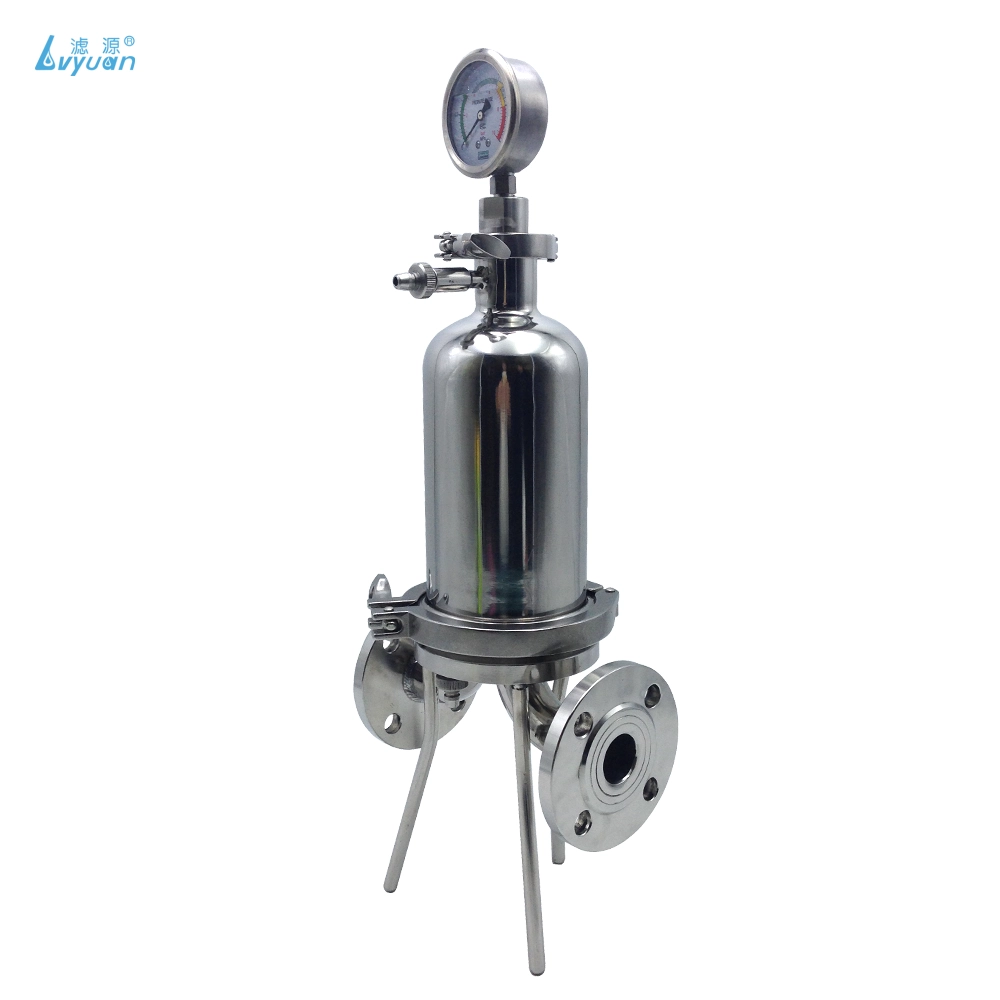
Sanitary filter housing
This filter housing will allow you to filter large volumes of nanoemulsion with ease. Sanitary vent and drain valves permit easy venting, draining, sampling, or integrity testing operations. The new cartridge locking design features additional cut-outs for traditional half-moon portions of the Code 7 bayonet locks, enhancing clean ability and drain ability.
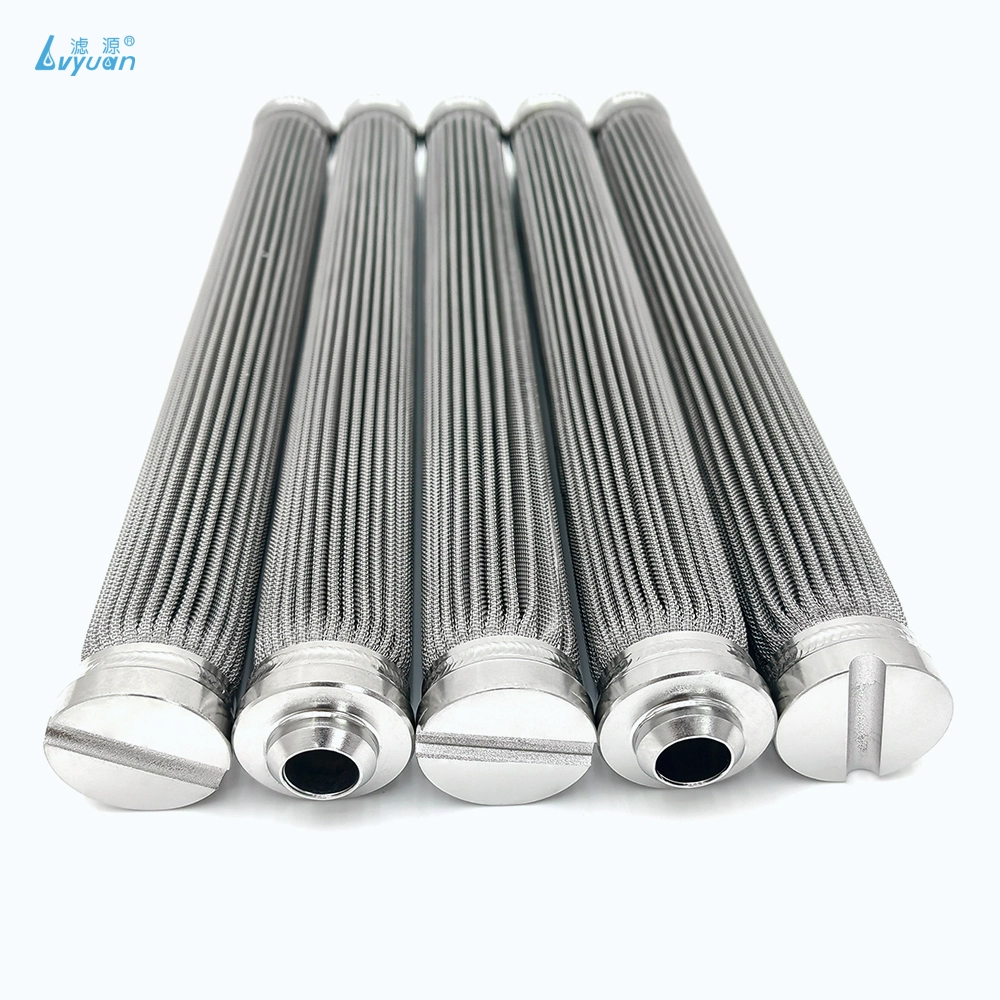
Stainless steel pleated filter cartridge
Lvyuan Stainless Steel Pleat Filter Cartridge constructed from high-quality SS 304 or SS 316L material, this filter exhibits exceptional resistance to high temperatures and rust.
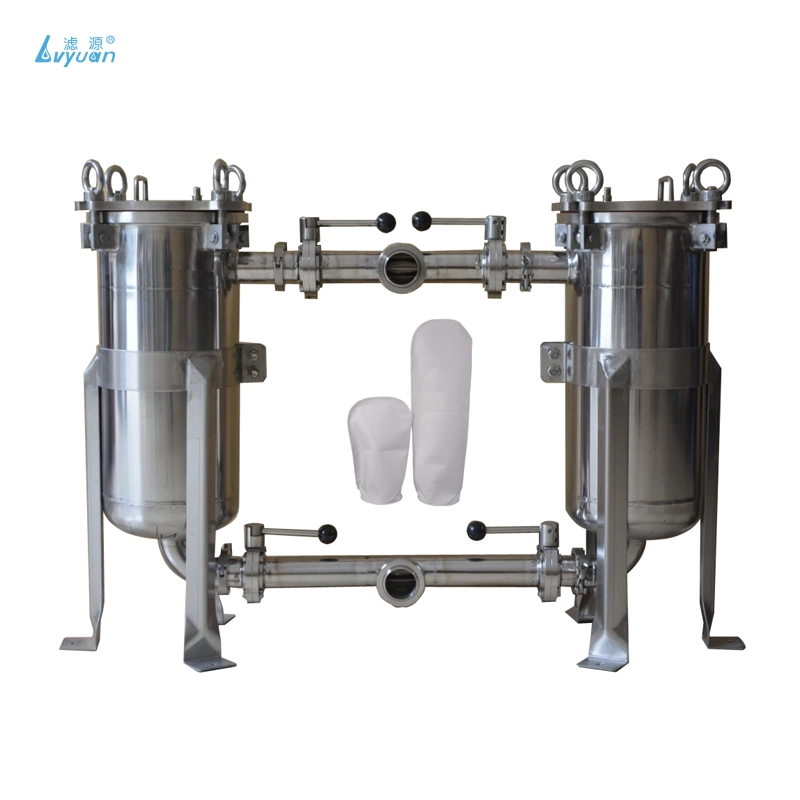
Stainless Steel Duplex filter housing
As the manufacturer, we offer a comprehensive range of Duplex Filter Housings designed to provide efficient and reliable filtration solutions for various industrial applications.
© 2024 Lvyuan All Rights Reserved. | Privacy policy • Terms and conditions