Understanding Metal Transformation During Sintering | Lvyuan
What Happens to the Metal During Sintering?
The sintering process is a fascinating field of study in materials science, especially for those in the business of producing sintered materials like Lvyuan. This process might seem mysterious to some, but understanding it is crucial for industries that rely on high-quality filtration solutions. As a pioneering filter manufacturer, Lvyuan stands at the forefront, using its extensive expertise to transform raw metals into functional components. Let’s explore the intricacies of what happens to metal during sintering and how Lvyuan capitalizes on this process to deliver top-notch sintered filters.
Introduction to Sintering
Sintering is a thermal process that fuses particles of metal together without reaching the point of liquefaction. Traditionally used in metallurgy, this method enhances the properties of materials, imparting them with enhanced structural integrity and performance. During sintering, powdered metal is compacted and heated to just below its melting point. This process results in particles bonding together, leading to the formation of a solid piece.
For an industry leader like Lvyuan, understanding the nuances of sintering is not just about scientific curiosity; it’s essential for creating robust, durable, and efficient filters capable of handling various industrial applications.
The Process of Sintering: Step-by-Step
1. Powder Preparation: The first phase involves selecting and preparing the metal powder, ensuring it has the correct particle size and composition.
2. Compaction: The metal powder is pressed into a mold under high pressure to form a compact shape, known as a green body.
3. Heating: The compacted metal is heated in a furnace at temperatures below its melting point, triggering diffusion processes.
4. Bonding: During heating, atoms at grain boundaries start to diffuse, leading to the densification and bonding of particles.
5. Cooling: The sintered metal is slowly cooled to retain structural integrity, resulting in a solid, cohesive structure.
These steps enhance the density, strength, and thermal conductivity of the material while retaining porosity, which is particularly valuable in filtration applications.
Benefits of Sintering Metal
The sintering process offers numerous advantages that are essential to Lvyuan’s product line:
- Improved Mechanical Properties: Sintering increases the strength and durability of metals, which is vital for creating long-lasting filters.
- Enhanced Control Over Porosity: The ability to control the level of porosity allows for precise filtration solutions tailored to specific industrial needs.
- Cost-Effectiveness: Sintering can be more economical compared to other metal processing methods, reducing waste and material costs.
- Versatility: This process is suitable for a broad range of metals and alloys, granting Lvyuan flexibility in design and application.
Lvyuan’s Commitment to Quality Through Sintering
At Lvyuan, we believe in leveraging the sintering process to its fullest potential. Our commitment to delivering industry-leading filtration solutions is reinforced by in-depth research and innovation in sintering technology. Here’s how we maintain our edge:
- State-of-the-Art Facilities: Our advanced manufacturing units in China are equipped with the latest technology, ensuring precision in every sintered product.
- Rigorous Quality Control: Each step of our sintering process is meticulously monitored to uphold our high standards of quality.
- Customized Solutions: We offer bespoke sintering services, tailoring our products to meet unique customer requirements across various industries.
Frequently Asked Questions
Q1: How does sintering affect the metal's porosity?
Sintering allows control over porosity levels, which is crucial for applications like filtration that demand specific pore sizes.
Q2: Is sintering an environmentally friendly process?
Yes, sintering is efficient and has a low environmental impact due to reduced waste and energy consumption compared to traditional smelting.
Q3: What metals are commonly used in sintering?
Common metals include stainless steel, bronze, and titanium, each chosen based on the specific application needs and desired properties.
Q4: How does Lvyuan ensure consistency in sintered filter quality?
Through strict quality checks and continuous R&D, Lvyuan ensures each filter meets stringent quality standards.
Conclusion
Understanding what happens to the metal during sintering opens up incredible opportunities for innovation in industrial applications. Lvyuan’s use of sintering technology not only exemplifies our commitment to quality but also highlights our role as leaders in the filtration industry. By mastering the art of sintering, we continue to deliver exceptional, customized, and efficient solutions to meet the diverse needs of our clients. With continuous advancements and a keen focus on quality, Lvyuan remains at the forefront of the sintered filter market, ensuring excellence in every product.
Embrace the future of filtration with Lvyuan, where tradition meets cutting-edge technology.
Custom sintered metal candle filter Manufacturers and suppliers
20 Questions for Sintered Metal Filters - Lvyuan
Custom sinter filter Manufacturers and suppliers
What Are the Standards for Sintered Metal Filters? | Lvyuan
Sintered Metal Filters
Can sintered metal filters be customized for specific applications?
Yes, sintered metal filters can be customized based on shape, size, material, filtration accuracy, and other specifications to meet the unique requirements of different applications.
Metal mesh filters
What are the key advantages of sintered wire mesh filter?
• High Strength: The sintered wire mesh filter exhibits excellent mechanical strength.
• Uniform Porosity: The sintering process creates a uniform pore structure for efficient filtration.
• Temperature Resistance: Suitable for applications with high temperatures.
• Easy to Clean: Can be cleaned and reused multiple times.
• Chemical Resistance: Resistant to corrosion and chemical exposure.
What maintenance is required for sintered wire mesh filter?
Regular cleaning is the primary maintenance for sintered wire mesh. The cleaning frequency depends on the application and the type of contaminants being filtered. Follow the manufacturer's guidelines for proper maintenance.
Stainless Steel Cartridge Filter Housing
What are the benefits of using stainless steel cartridge filter housings?
Stainless steel cartridge filter housings offer corrosion resistance, durability, and hygiene, making them suitable for use in a wide range of industries, including food and beverage, pharmaceuticals, chemicals, and water treatment.
Porous Plastic Filter
How do I integrate sintered porous filter discs into my filtration system?
They are designed for easy integration into existing filtration systems. The compact design allows for straightforward installation and replacement.
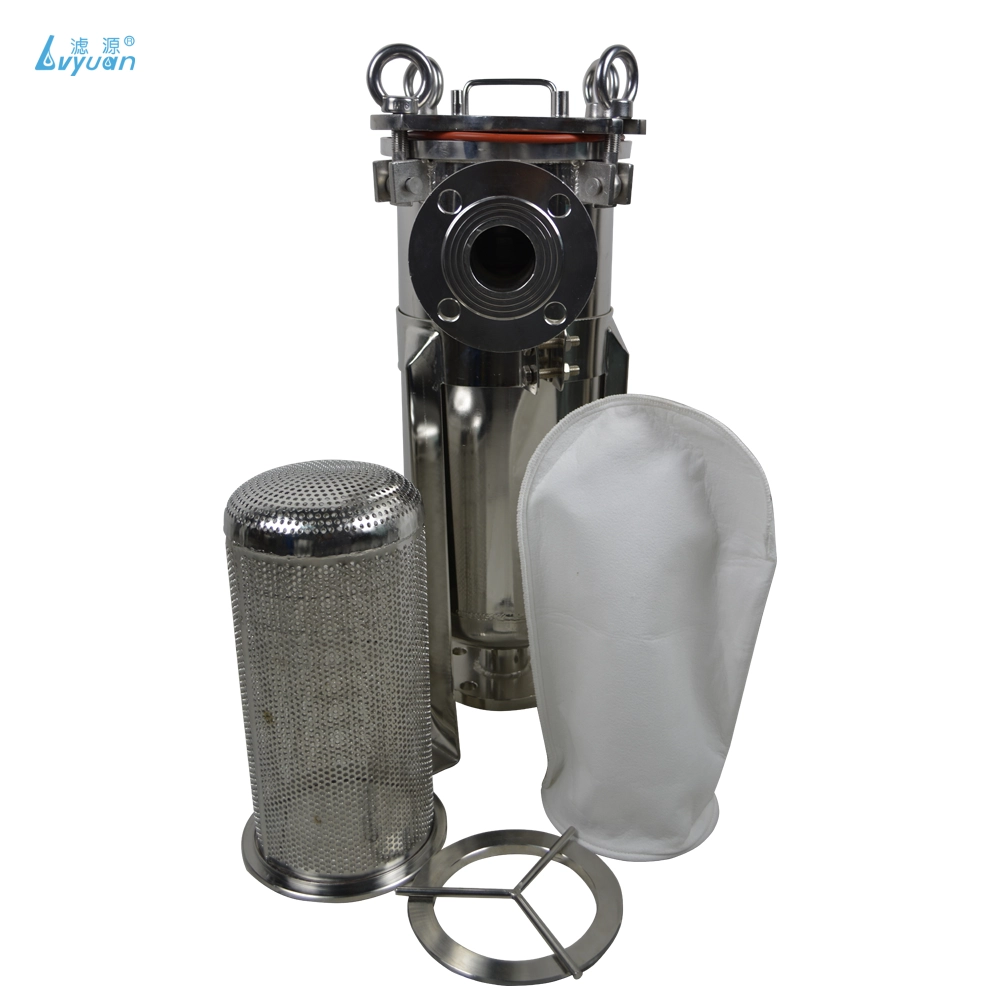
Bag filter housing
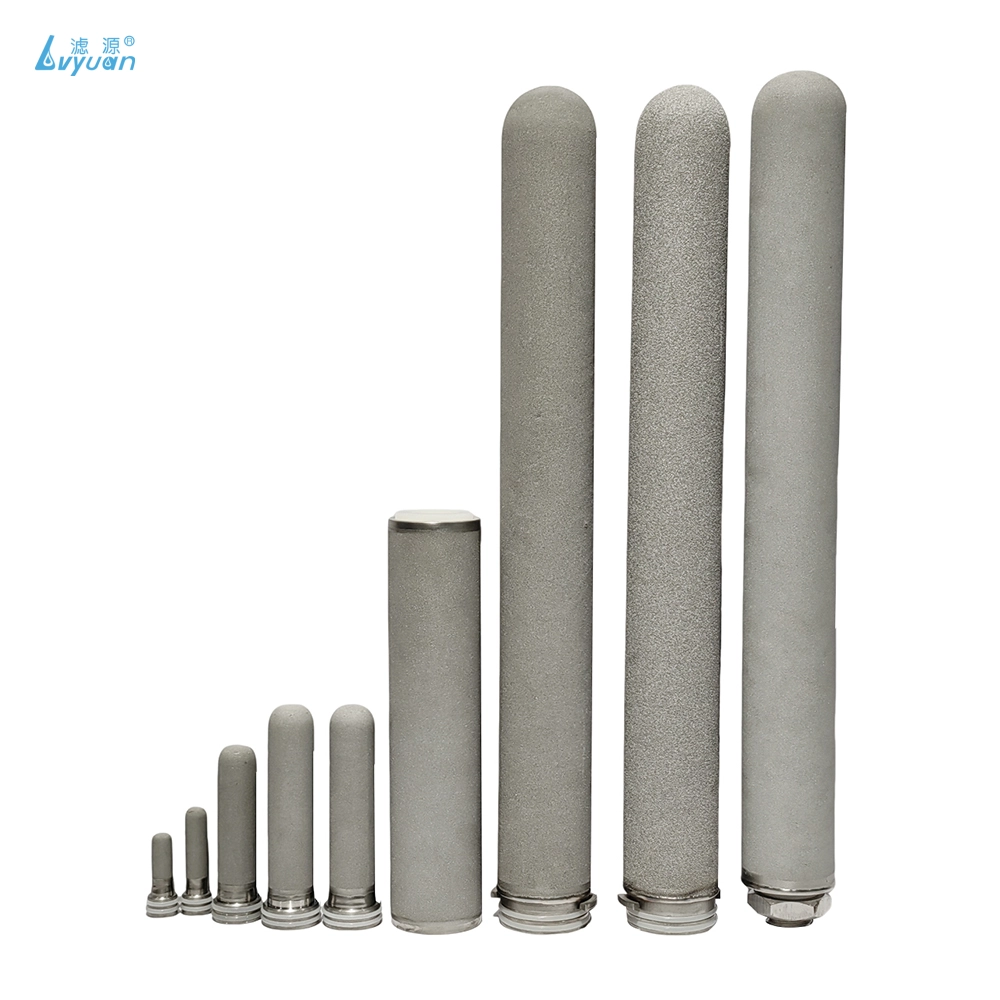
Sintered powder metal filters
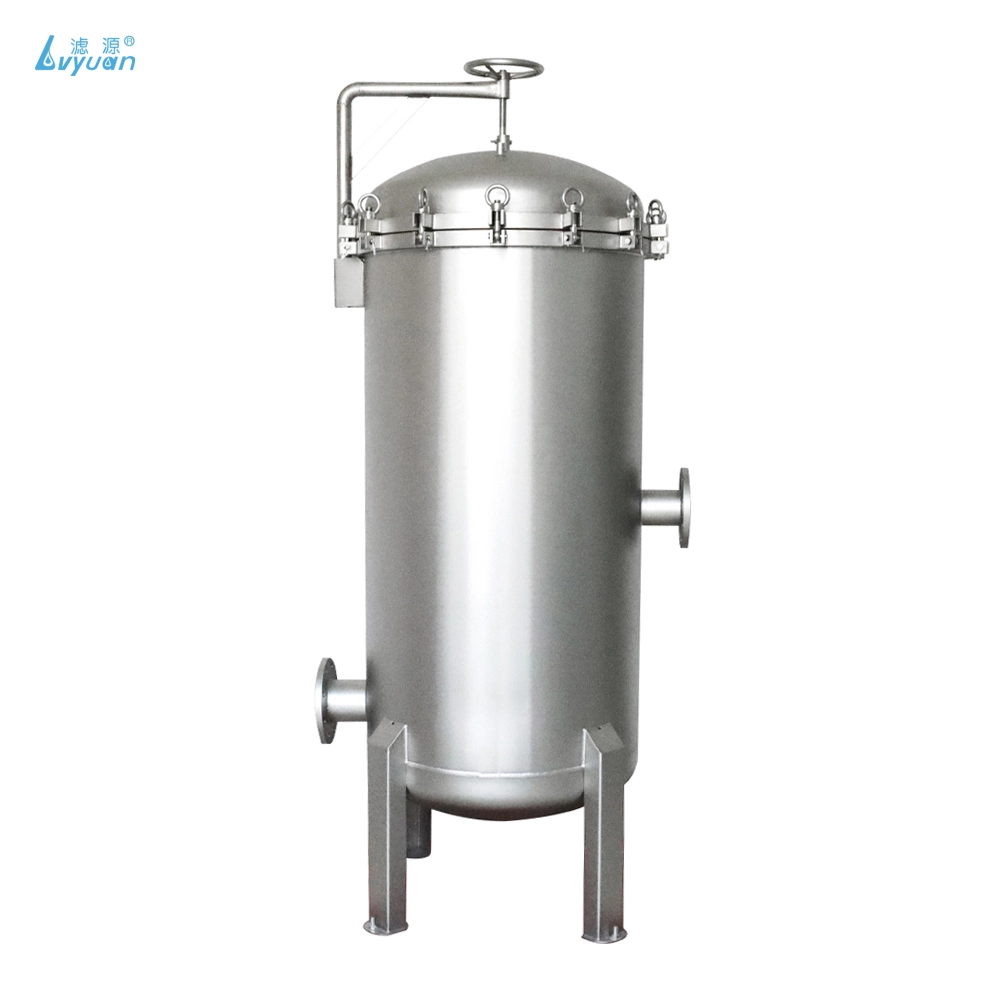
Stainless steel multi cartridge filter housing
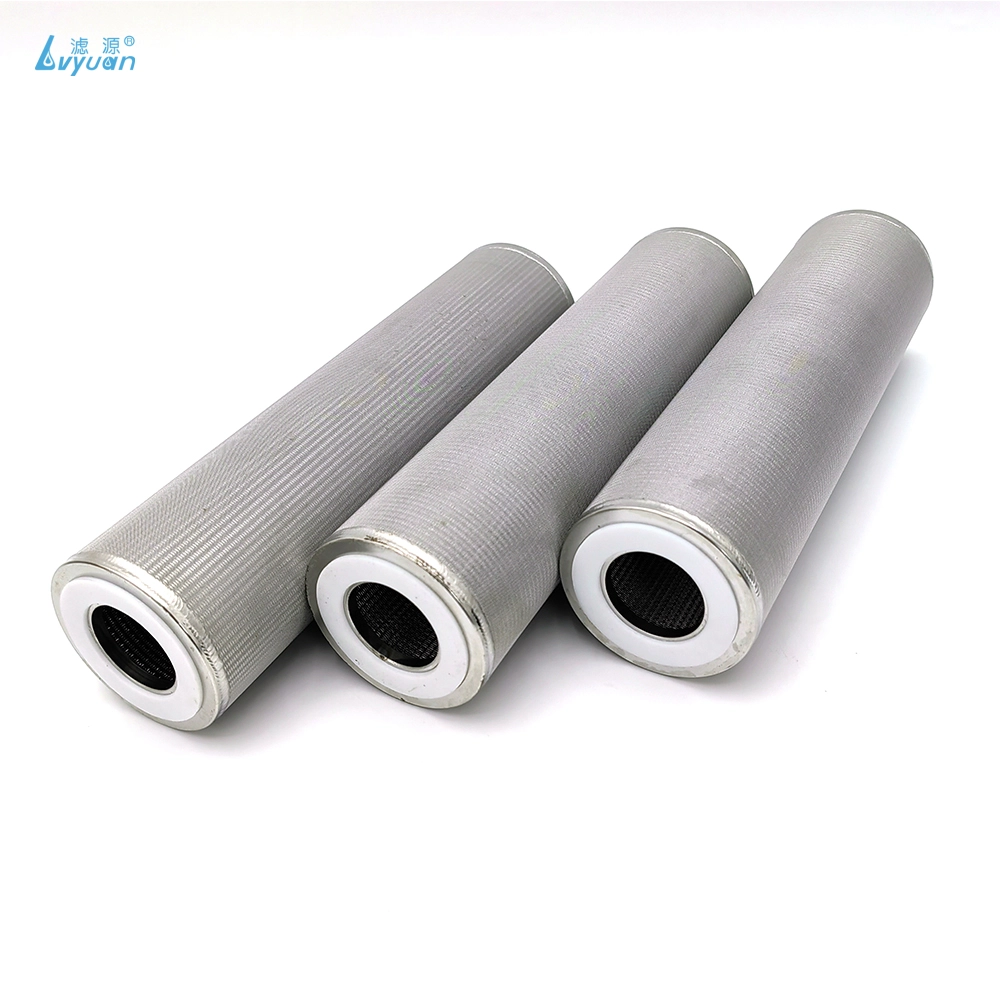
Sintered wire mesh filter
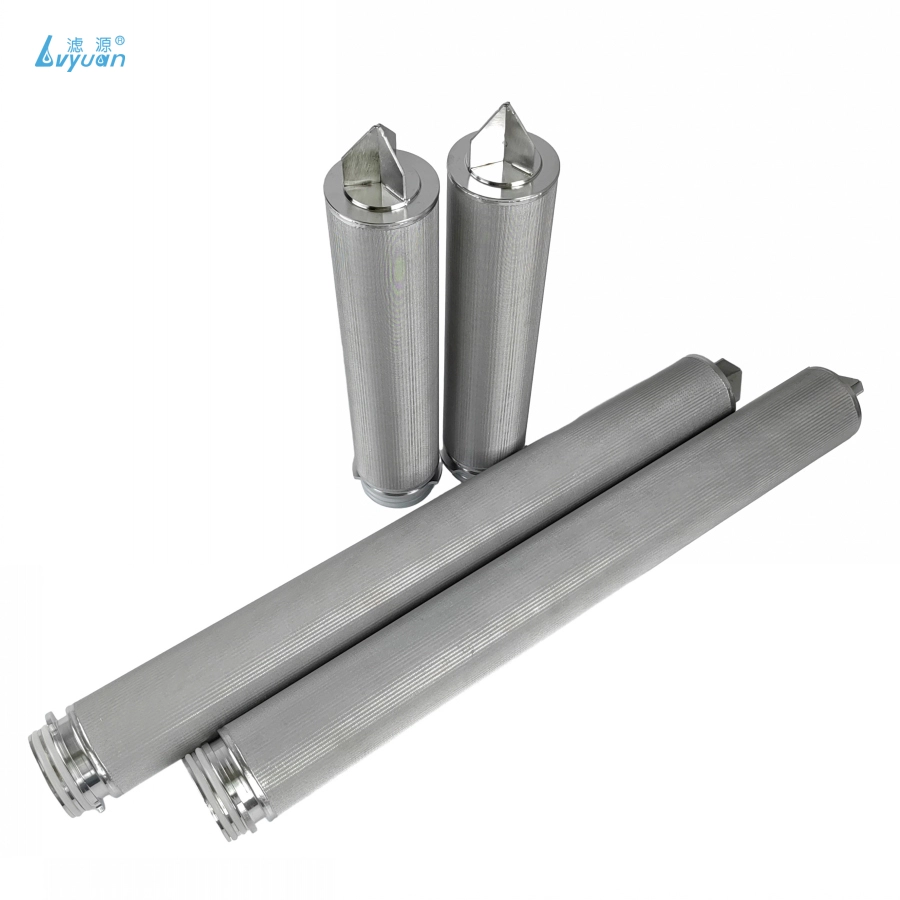
stainless steel filter water
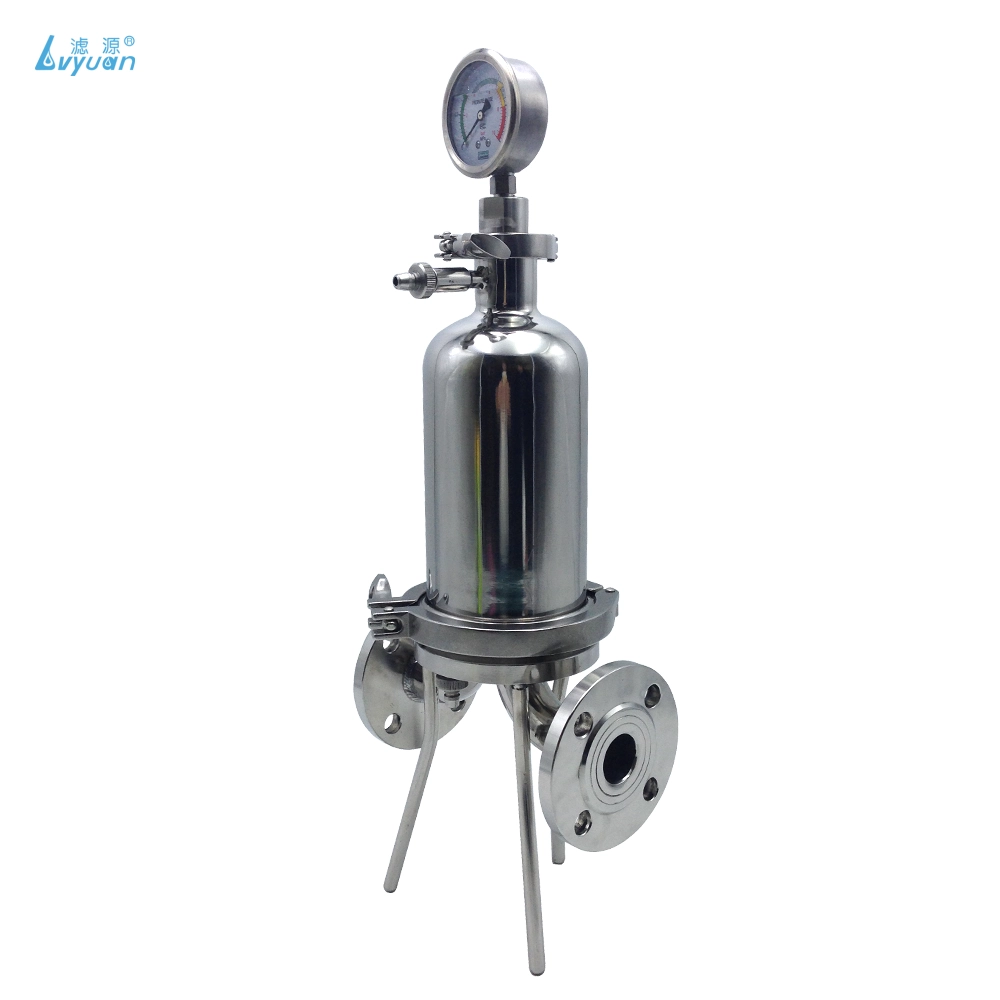
Sanitary filter housing
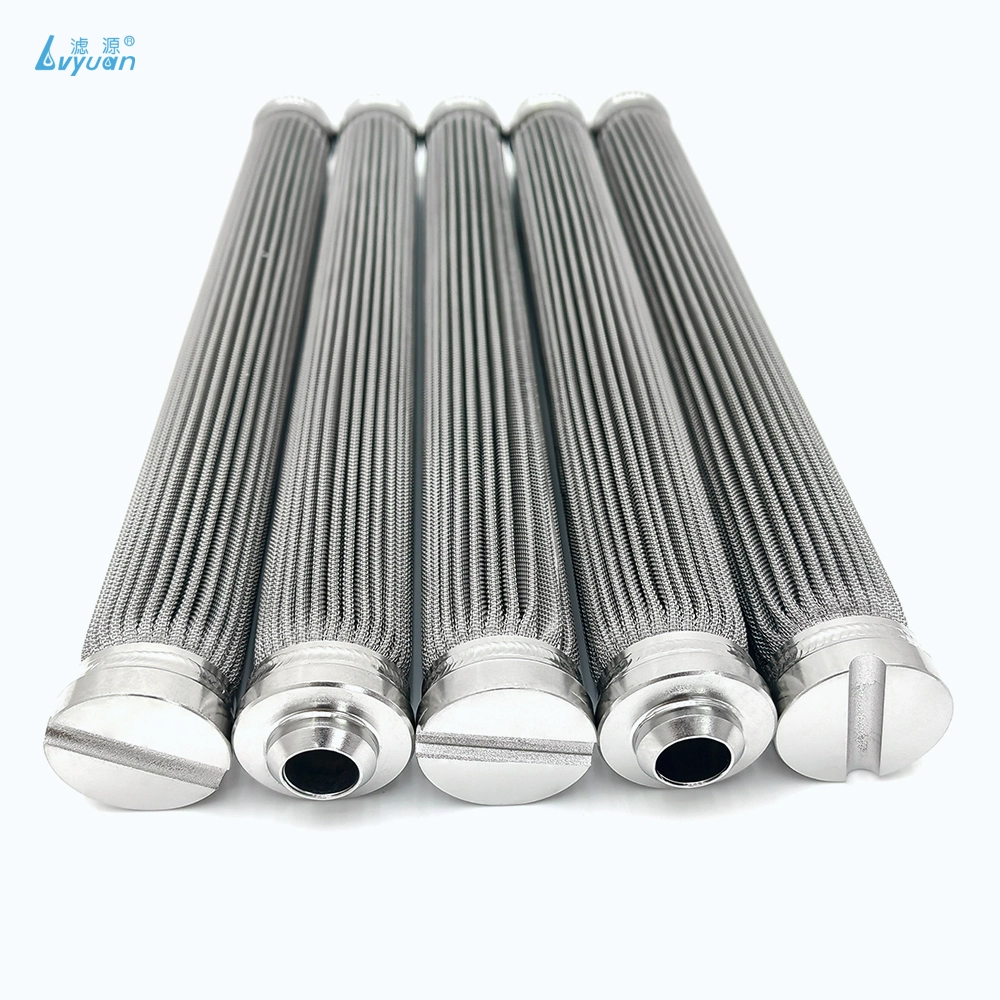
Stainless steel pleated filter cartridge
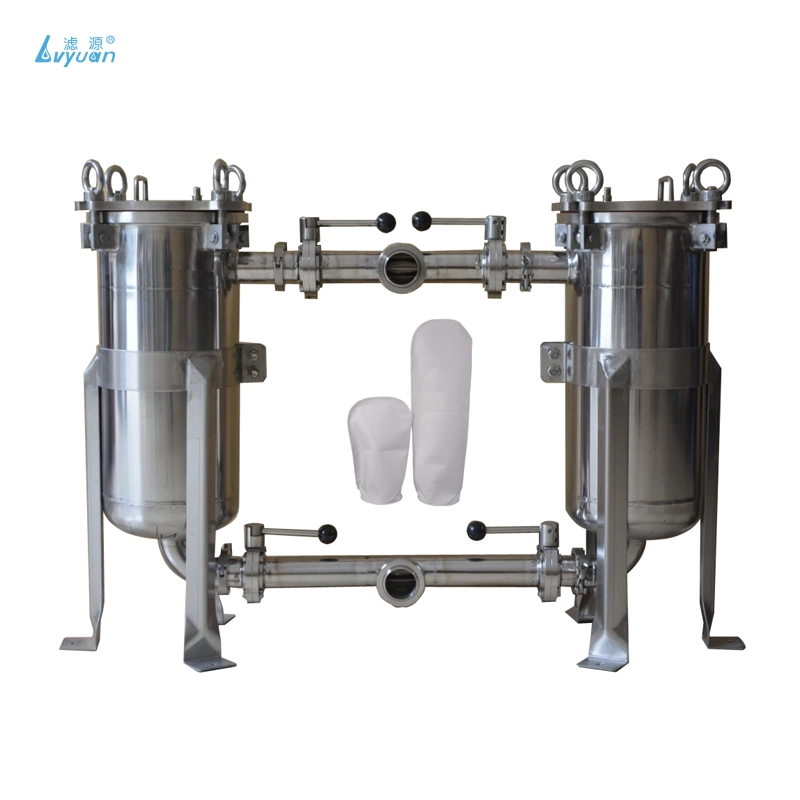
Stainless Steel Duplex filter housing
© 2024 Lvyuan All Rights Reserved. | Privacy policy • Terms and conditions