Understanding Chemical Industry Sintered Mesh Filter Cartridges
The functionality of chemical industry sintered mesh filter cartridges is based on the efficient filtration of micro porous mesh. Utilizing high-temperature sintering processes, suitable materials are formed into the structure of a micro porous mesh. These tiny channels allow liquids to pass freely while capturing microscopic particles, suspended matter, and other solid impurities.
The functionality of chemical industry sintered mesh filter cartridges is based on the efficient filtration of microporous mesh. Utilizing high-temperature sintering processes, suitable materials are formed into the structure of a microporous mesh. These tiny channels allow liquids to pass freely while capturing microscopic particles, suspended matter, and other solid impurities. This ensures the purity of liquids in chemical production processes, preventing impurities from impacting product quality and production equipment.
Applications
1. Chemical Raw Material Preparation:
Removes tiny particles from raw materials, ensuring the purity of prepared materials.
2. Solvent and Solution Treatment:
Used in the treatment of solvents and solutions in chemical production, eliminating impurities and particles.
3. Coating and Paint Production:
Filters solid particles from pigments and coatings during the production of coatings and paints, enhancing product quality.
4.Polymer Production:
Removes microscopic particles from reaction products in polymer production, ensuring polymer purity.
5. Chemical Wastewater Treatment:
Used in wastewater treatment to eliminate suspended matter and impurities, purifying wastewater.
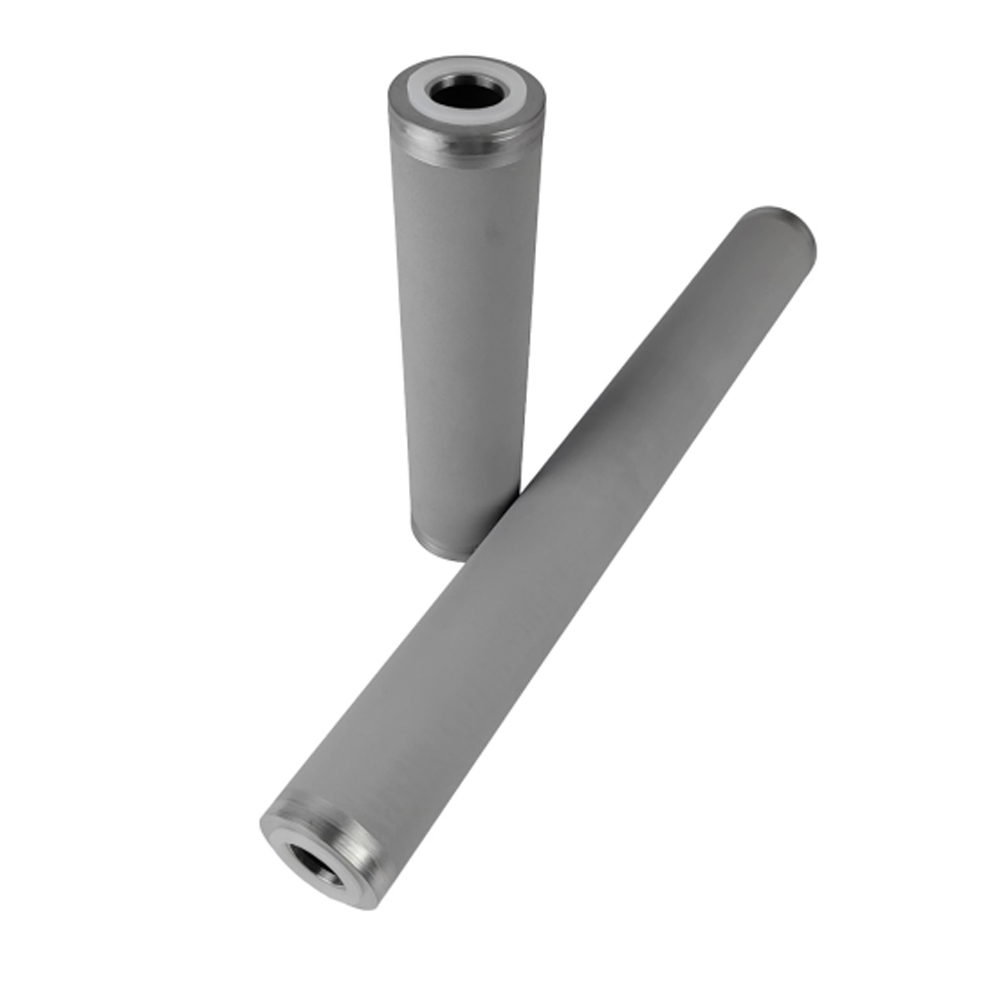
Features and Advantages
• Corrosion Resistance:
Manufactured using corrosion-resistant materials suitable for corrosive media in chemical production.
• High Filtration Precision:
Achieves submicron-level filtration precision, removing tiny particles and microorganisms.
• High-Temperature Resistance:
high-temperature sintering process imparts high resistance to elevated temperatures, making it suitable for high-temperature chemical production environments.
• Long Service Life:
Typically has a longer lifespan, reducing the frequency of replacements and lowering maintenance costs.
• High Flow Rate:
Some well-designed sintered mesh filter cartridges can achieve high-flow filtration, ensuring efficient chemical production processes.
Maintenance and Replacement
To ensure the efficient operation of chemical industry-sintered mesh filter cartridges, regular maintenance and cleaning are essential. Cleaning the filter surface or replacing the filter medium can prevent clogging, ensuring filtration efficiency. Maintenance frequency depends on the usage environment, such as particle concentration in the liquid and the characteristics of the chemical process.
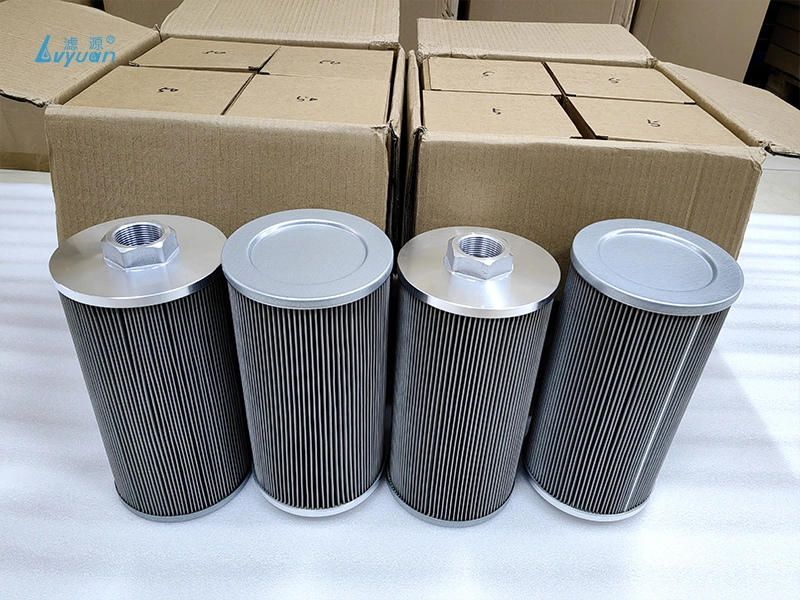
What is Sintered Metal Filter? Complete Guide by Lvyuan
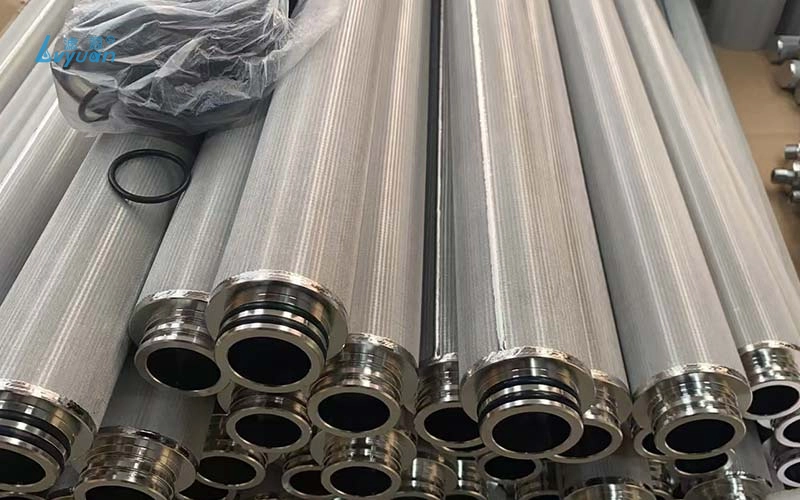
Sintered Filter Element Manufacturing Process and Applications
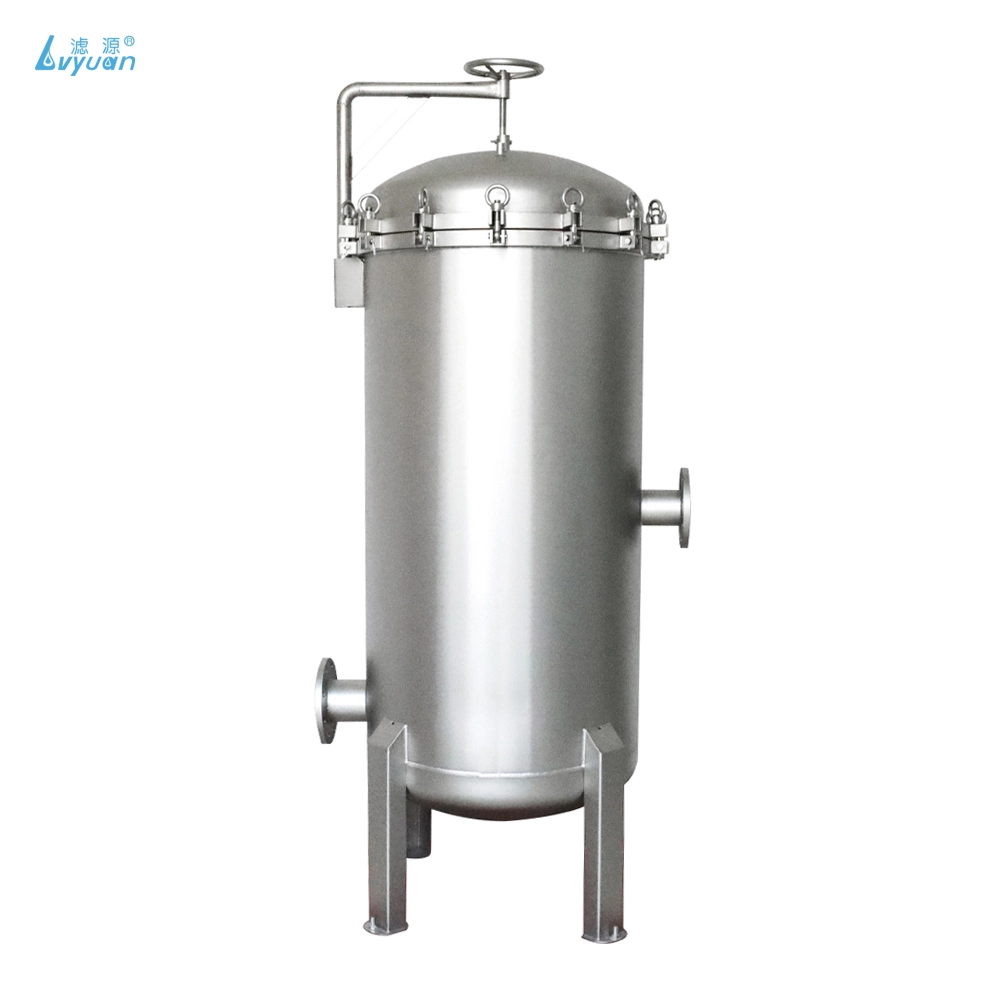
Applications of Sintered Metal Filters in Manufacturing
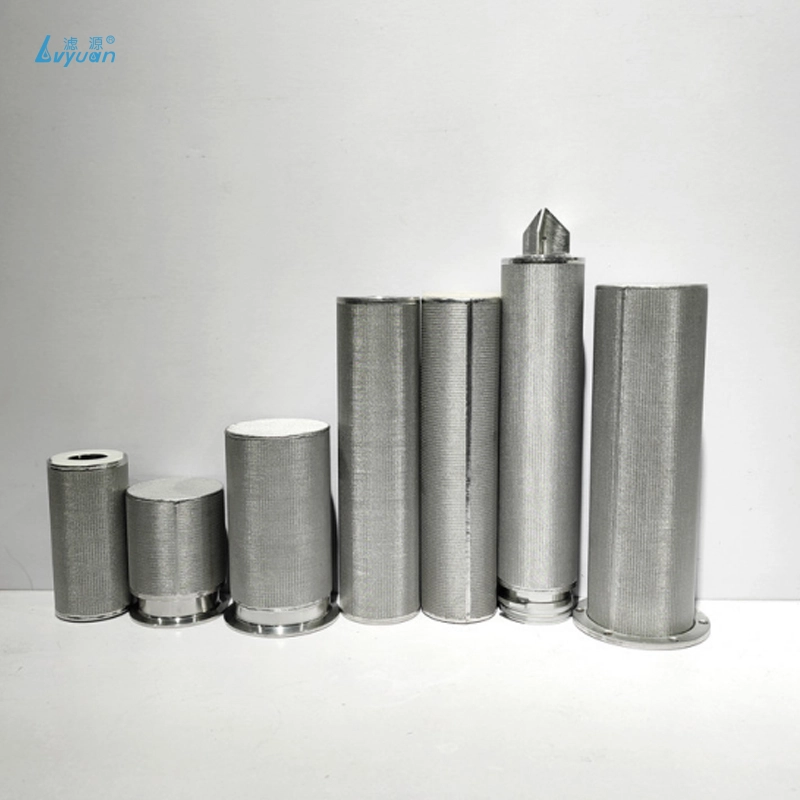
Why Lvyuan Is the Best China Manufacturer of Sintered Metal Filters
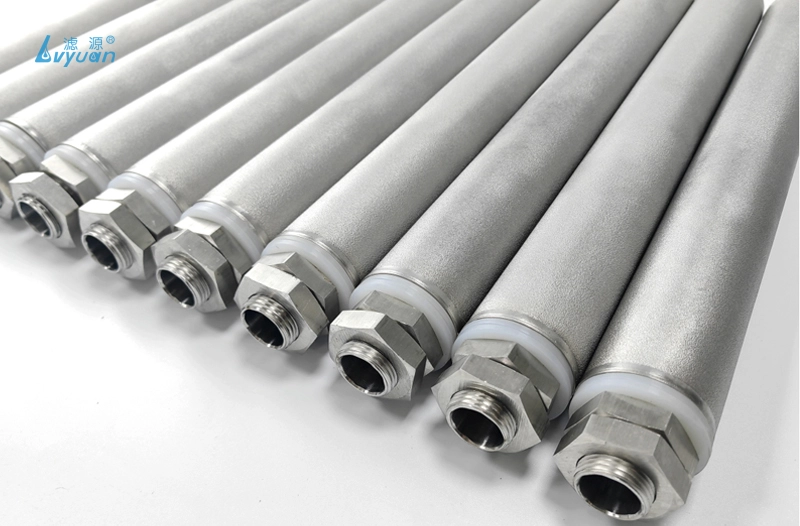
How to Clean Sintered Metal Filters: A Comprehensive Guide
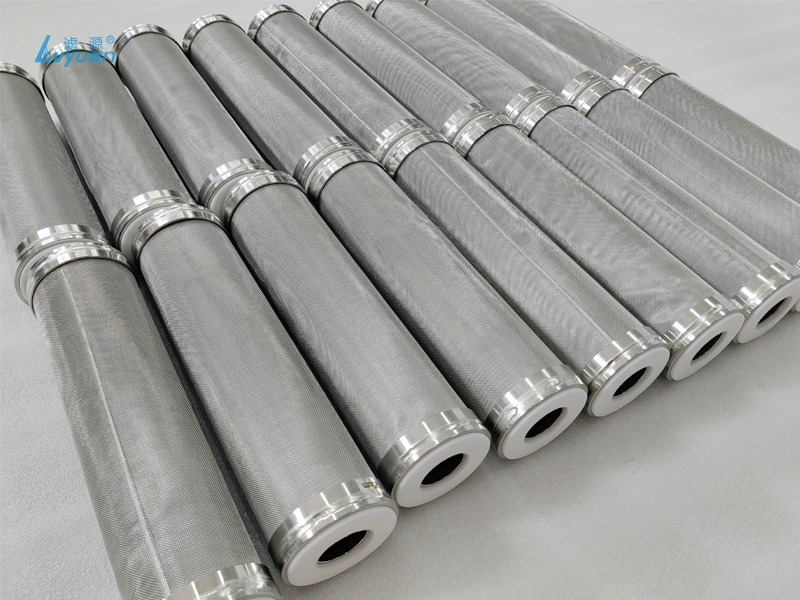
A Comprehensive Guide to Sintered Filters: Features, Production, and Benefits
For products
What are sintered metal filters?
Sintered metal filters are porous materials made by compacting and heating metal powders without melting them completely. The process results in a rigid structure with interconnected pores, offering filtration capabilities for various applications.
How are sintered metal filters cleaned?
Cleaning methods for sintered metal filters include backwashing, ultrasonic cleaning, and chemical cleaning. The method depends on the type of contaminants and the filter's specifications.
For company
How do you establish a long-term and positive business relationship?
We maintain high-quality standards and competitive prices to ensure mutual benefits for our customers. We treat every customer with respect, considering them not only as clients but also as friends. We engage in sincere business dealings and aim to build lasting friendships, regardless of their geographical location.
Stainless Steel Pleated Filter Cartridges
What industries commonly use Stainless Steel Pleated Filter Cartridges?
These cartridges find applications in a range of industries, including petrochemicals, manufacturing, food and beverage, pharmaceuticals, and more, owing to their versatility and efficiency in diverse filtration processes.
Are these pleat cartridges compatible with different filter media?
Yes, Stainless Steel Pleated Filter Cartridges are compatible with various filter media, providing flexibility to adapt to different filtration processes and substances.
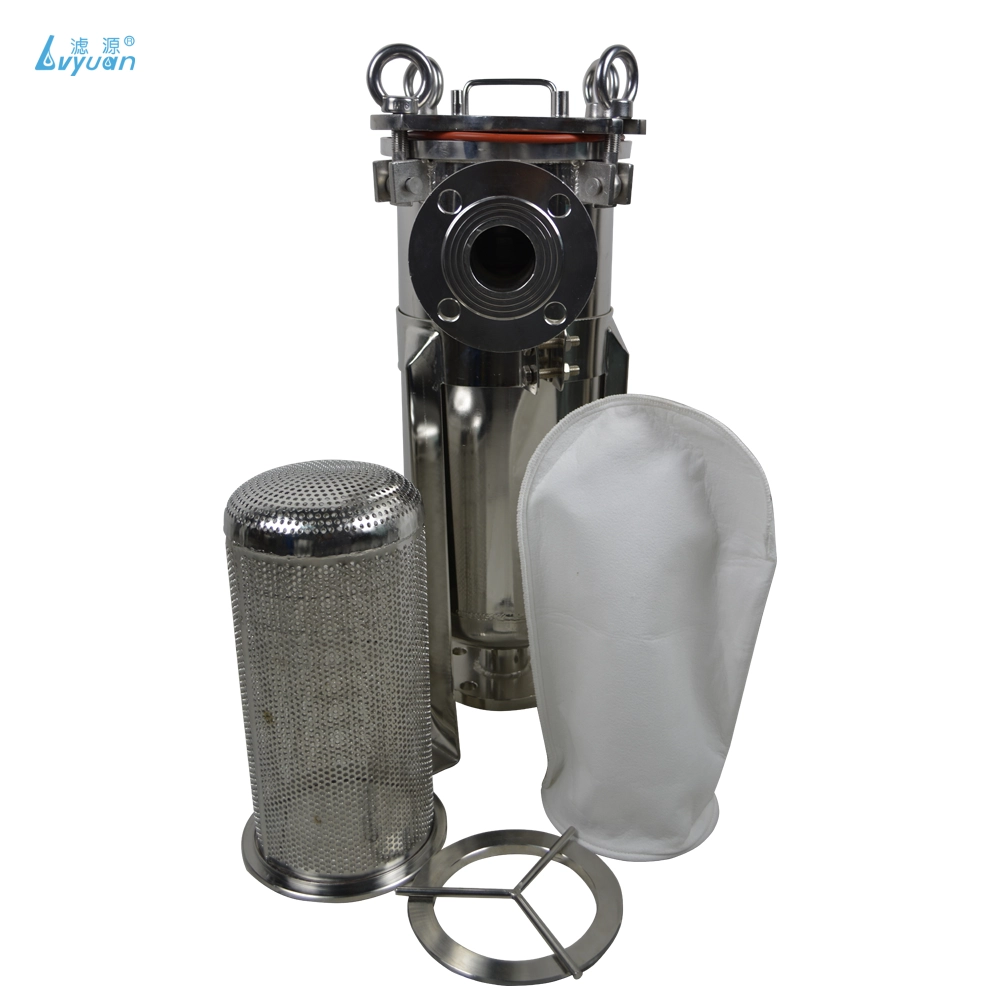
Bag filter housing
Bag filter housings are essential components in industrial filtration systems, designed to remove contaminants from liquids. To enhance the functionality and efficiency of bag filter housings, various features can be incorporated.
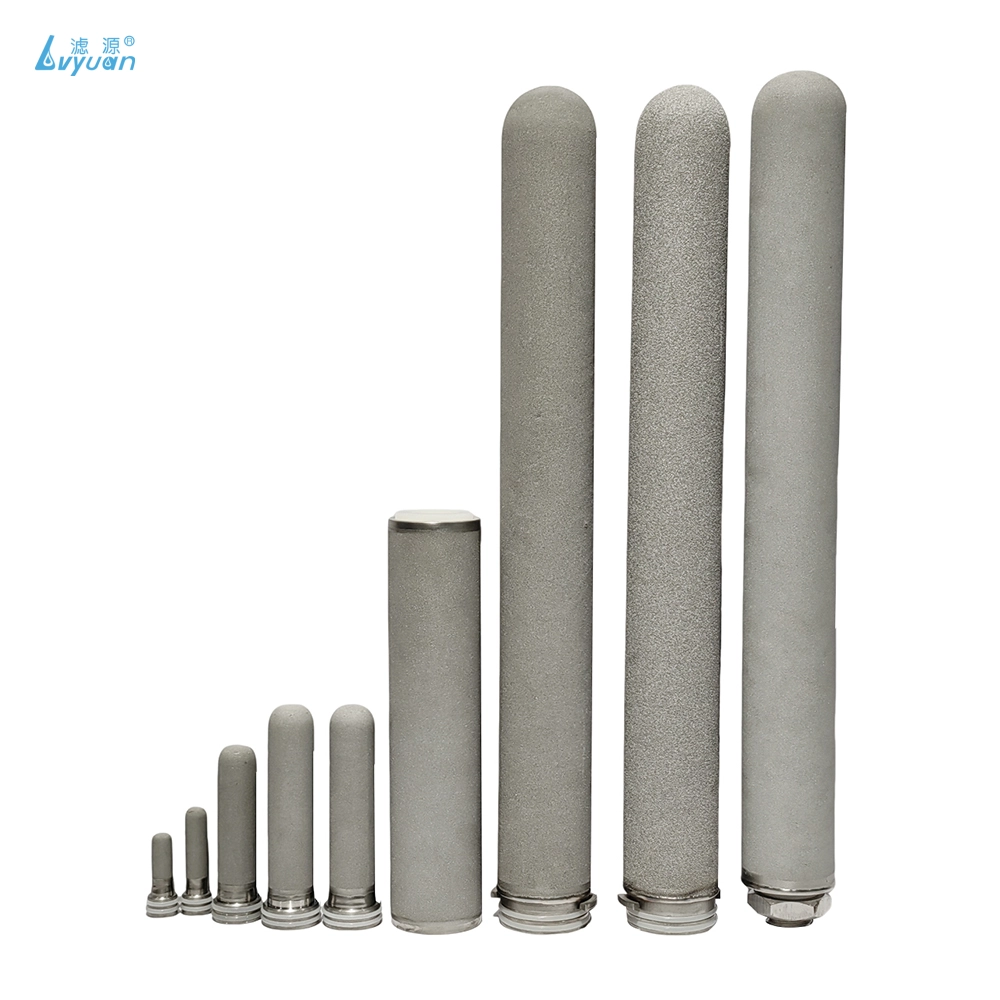
Sintered powder metal filters
Sintered powder metal filters are crafted from compressed and sintered metal powders, forming a porous structure. Porosity: 28%-50% Permeability: 0.02-20L/cm²minPa Pressure Resistance: 0.5Mpa Temperature Resistance: Less than 280℃
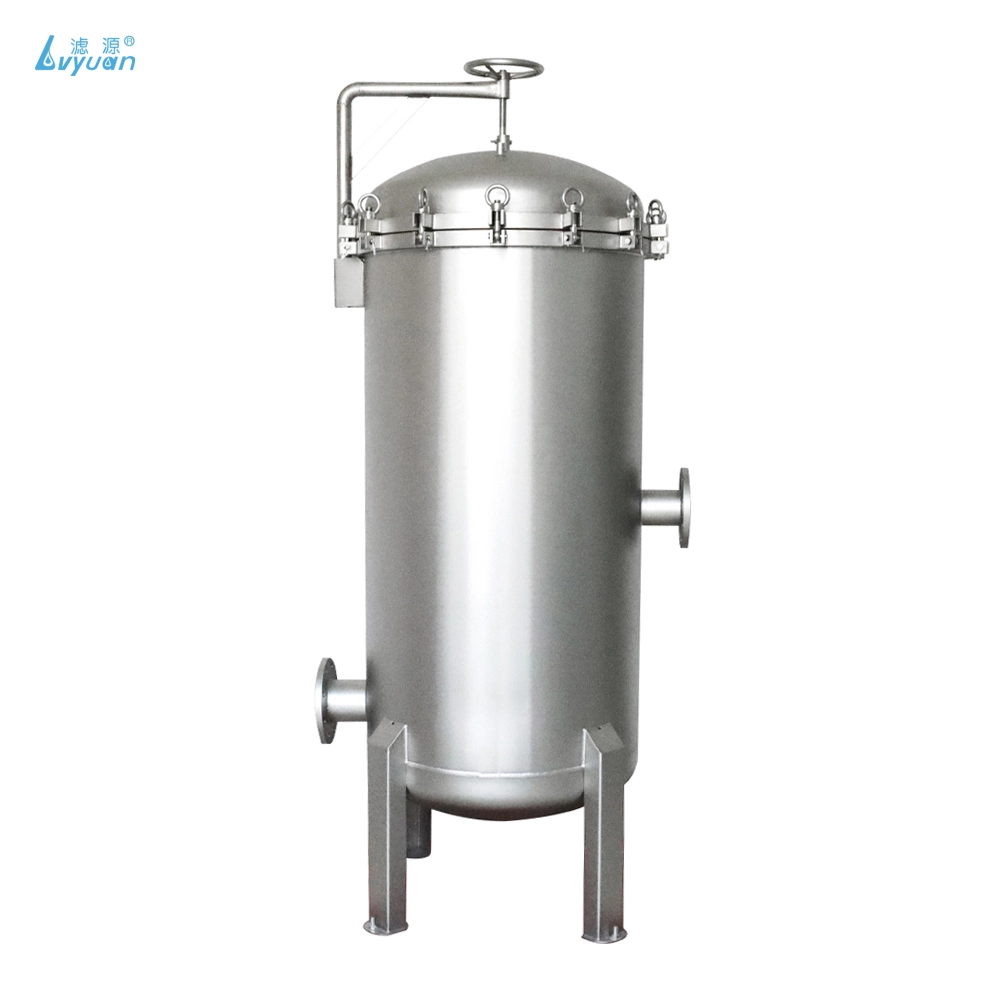
Stainless steel multi cartridge filter housing
Discover unparalleled filtration efficiency with our Stainless Steel Multi Cartridge Filter Housing – a testament to precision engineering and reliability.
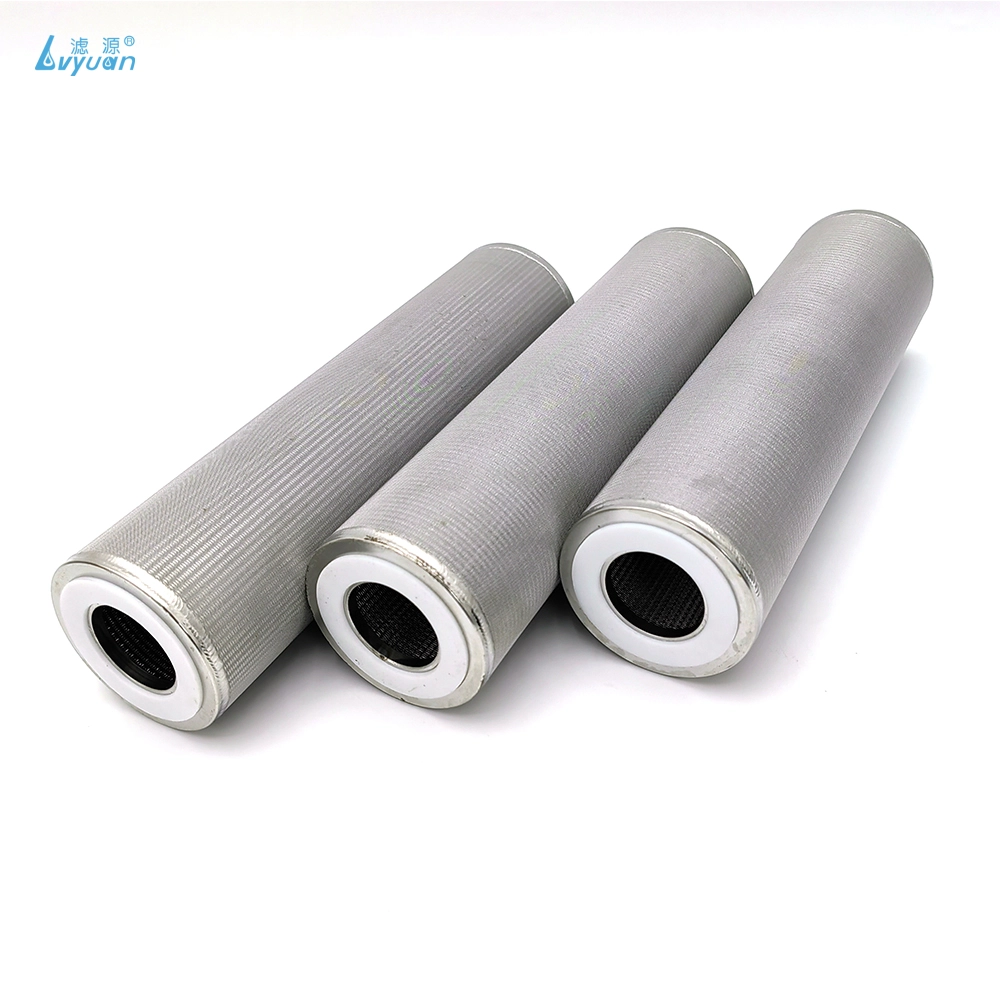
Sintered wire mesh filter
Benefit from outstanding high-pressure resistance and consistent filtration efficiency with Lvyuan's sintered metal mesh. Our sintered wire mesh finds versatile applications in diffuser screens, centrifuges, breather vents, fluidized beds, chromatography, polymer processing, petrochemical industries, hydraulic filters, and more.
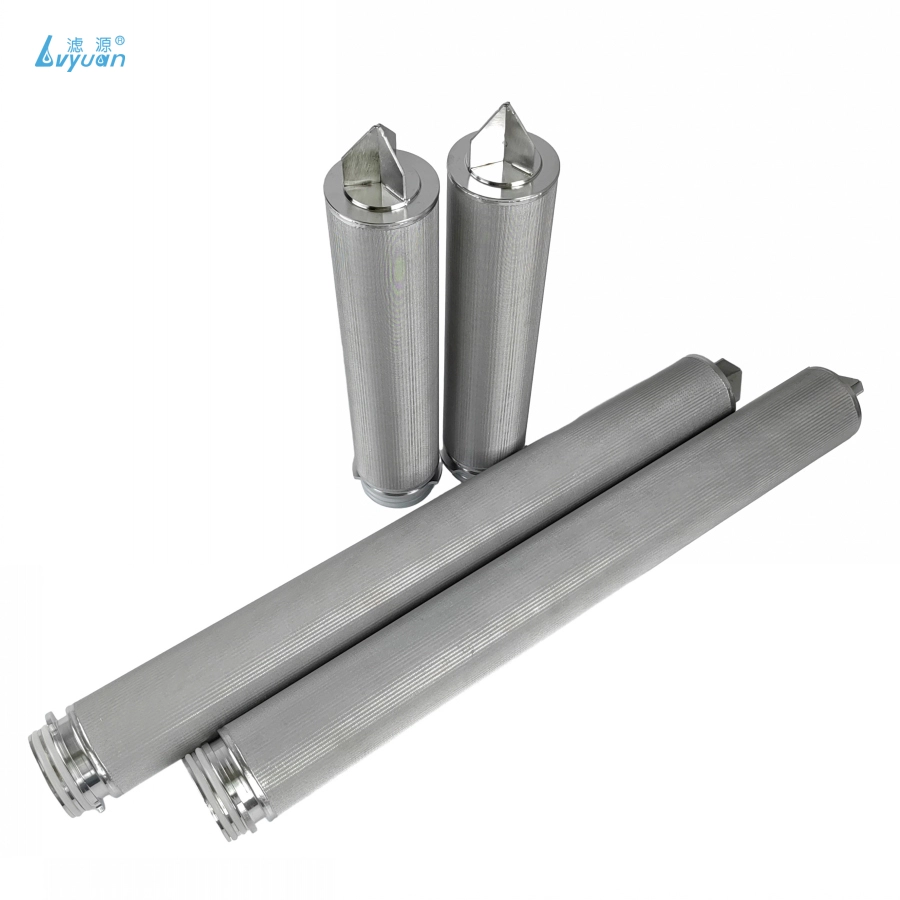
stainless steel filter water
Lvyuan’s sintered stainless steel filter stands as a pivotal filtration element crafted through a meticulous sintering process, with stainless steel serving as the core material.
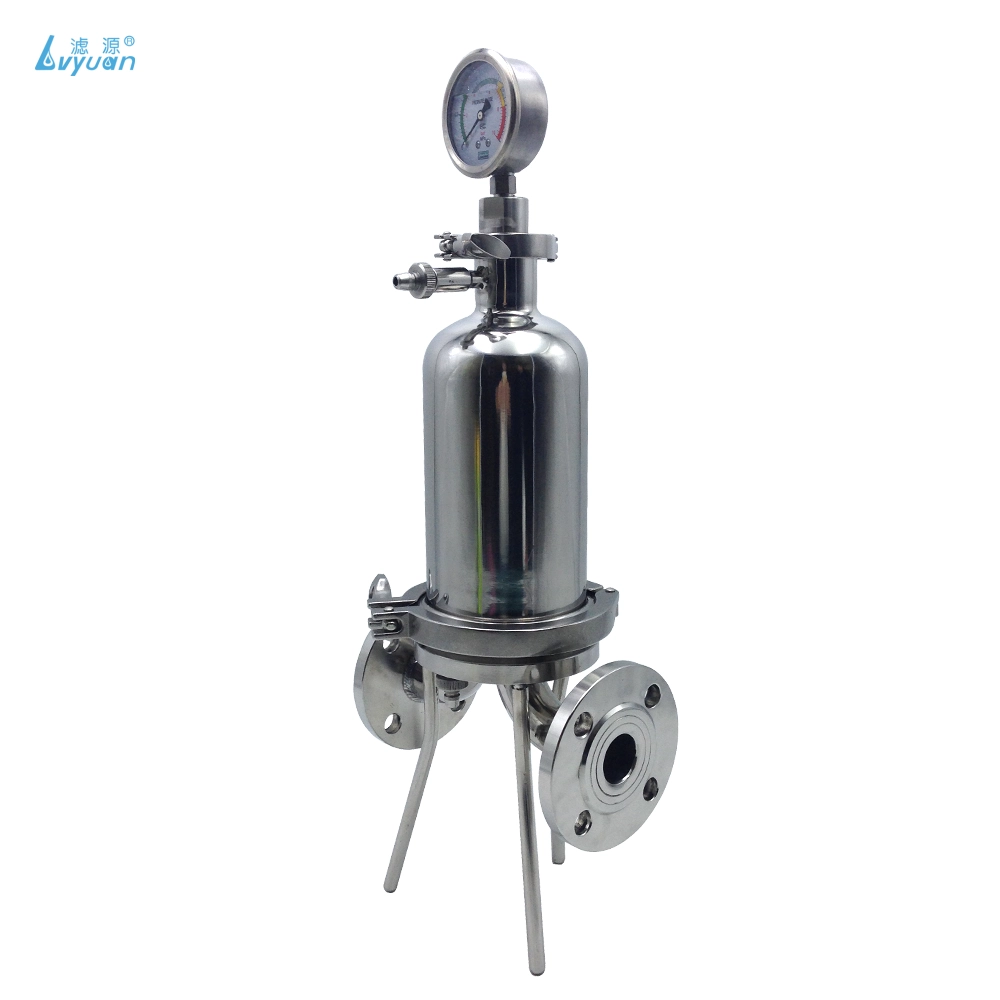
Sanitary filter housing
This filter housing will allow you to filter large volumes of nanoemulsion with ease. Sanitary vent and drain valves permit easy venting, draining, sampling, or integrity testing operations. The new cartridge locking design features additional cut-outs for traditional half-moon portions of the Code 7 bayonet locks, enhancing clean ability and drain ability.
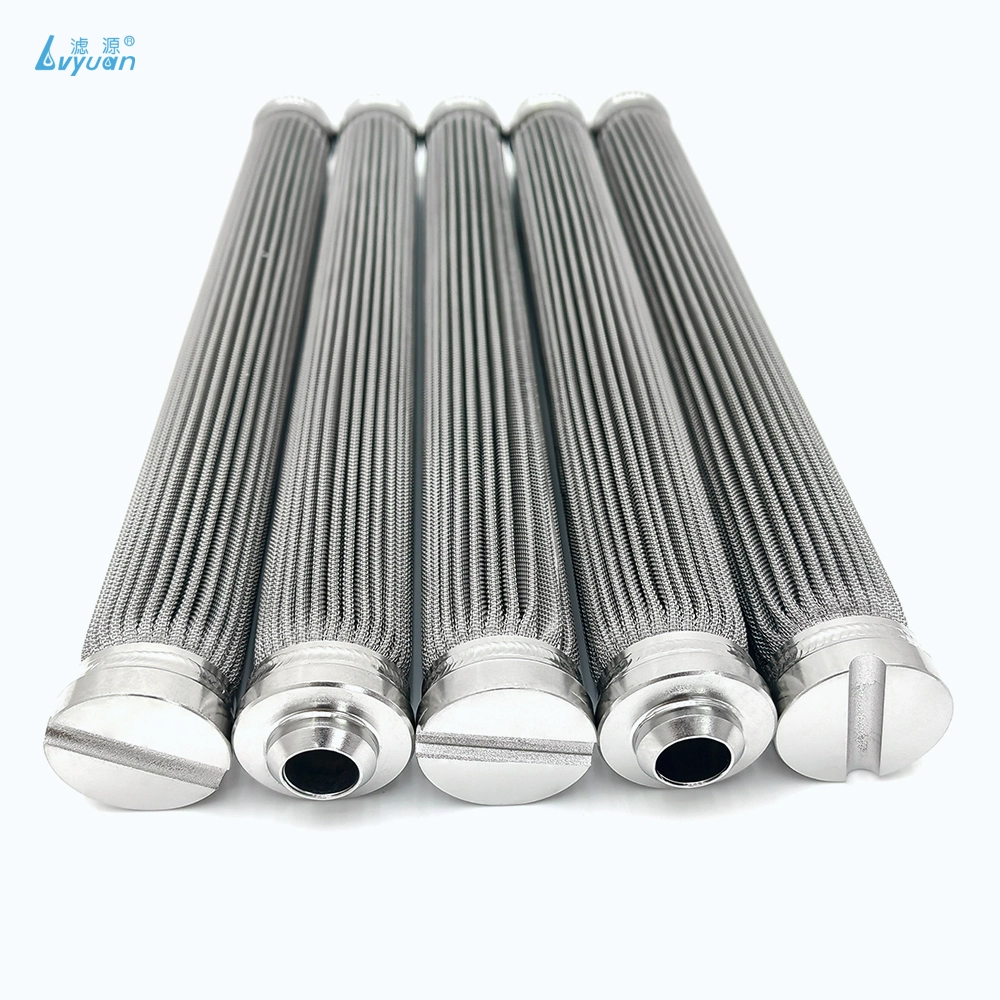
Stainless steel pleated filter cartridge
Lvyuan Stainless Steel Pleat Filter Cartridge constructed from high-quality SS 304 or SS 316L material, this filter exhibits exceptional resistance to high temperatures and rust.
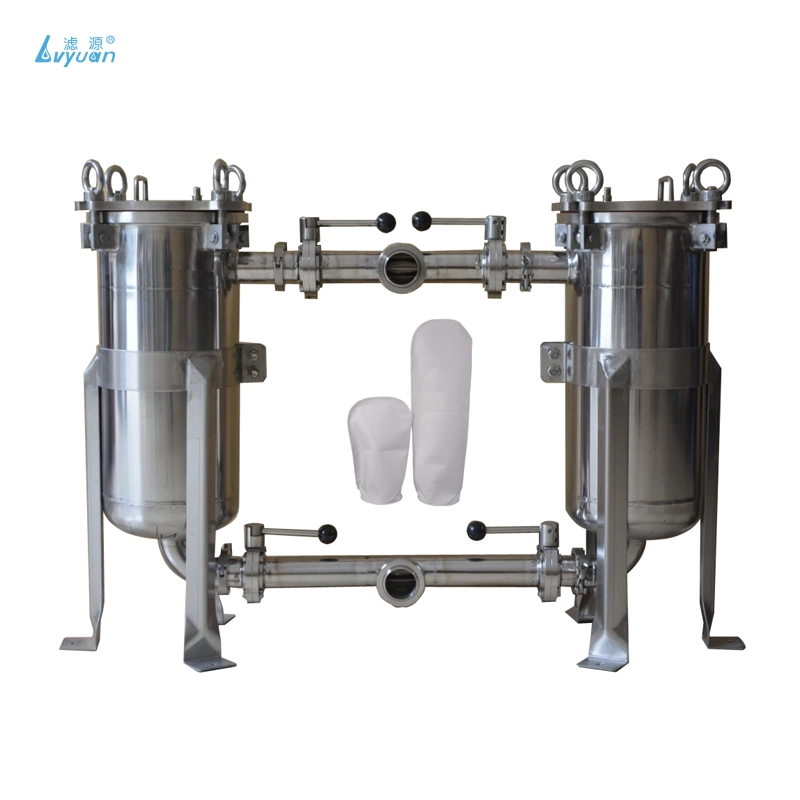
Stainless Steel Duplex filter housing
As the manufacturer, we offer a comprehensive range of Duplex Filter Housings designed to provide efficient and reliable filtration solutions for various industrial applications.
© 2024 Lvyuan All Rights Reserved. | Privacy policy • Terms and conditions